DIY metal bench lathe
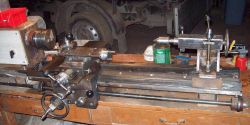
I was wondering if this design fits in this forum, but I can see that they were already similar, so it will be a bit of a change in this section.
Often I was faced with the problem of rolling a shaft (bushings, washers), and anyone who made extra money using the method: a drill mounted in a vice and a file or an angle grinder knows what the "torture path" is, not to mention the limitations of such a method.
Honestly, I initially wanted to buy a table lathe (ie TSB16), but practically all of them would be - as agreed, all of them were at the other end of Poland, and if it gets closer, the price is unacceptable.
So I decided to build from scratch, as is well known - you need a lathe to build a lathe but in my case this is not the case, for the construction I used only the hand tools available in almost every workshop.
Initially, I planned to make the spindle itself with a lathe chuck, so that the material could be processed with a file or grinder, then I tried to use a cross vise (which I had) as a support, the result - a failure.
Finally, I made a bed and a support from scratch, and then I could add new elements on it: gear, feed, tailstock.
DESCRIPTION:
Spindle - shaft on 2 tapered roller bearings, unfortunately not a through hole (I had one), but inside a 250mm fi25 hole.
Drive: 3-phase 0.55kW motor powered by an inverter and a single-stage gear with a ratio of approx. 1 / 2.6.
Bed - angle 120.
Lead screw - Tr20x4, cross slide and tailstock - Tr14x4 left-handed, tool sled - Tr12x3.
The bolts of the cross slide and the carriage are supported on both sides by thrust ball bearings, the lead screw from the right has 2 tapered bearings to eliminate the longitudinal play.
Longitudinal support - on the crank gear 17z to 34z and together with it 17z with a toothed rack module 1.5, which results in: 1 turn of the handle = 40.055mm.
The rest in the photo:
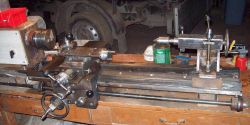
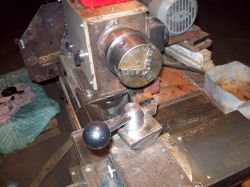
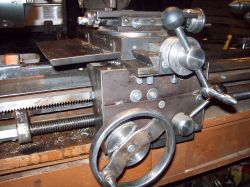
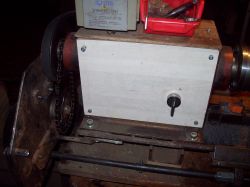
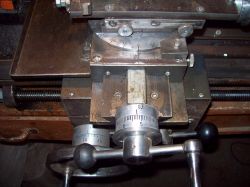

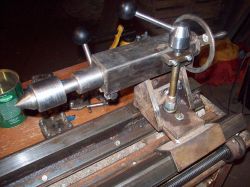
Here the guitar, gear spindle-intermediate shaft 1/2 chain, then toothed gear: two-stage for feed, and one-stage for threads (all pitches of metric threads can be obtained with one gear), for the 3rd photo setting for a pitch of 1 mm 14z / 28z plus the switch, i.e. left-hand thread in this case.
In the last photo, the larger threads are a typical M10, and the smaller one is M8x1 left.
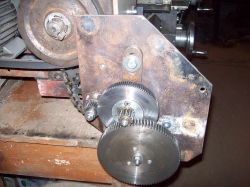
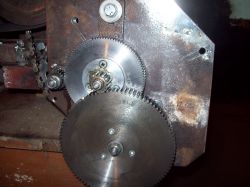
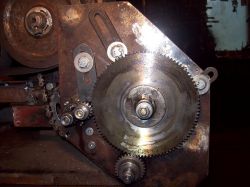
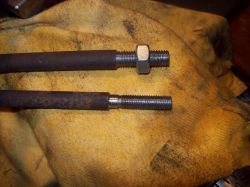
Rod fi 20 knife with plate and HSS
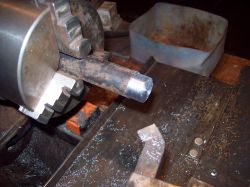
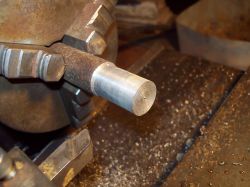
I know that it cannot be compared to the factory design, but not too large elements can be successfully re-threaded, the feeds are two (replacement of the gear on the intermediate shaft) with the diameter of the material, say fi 25 - max. thickness per one pass is about 0.6..0.7mm - with a feed rate of 0.05mm / rev.
Maybe someone has built similar devices and will share suggestions on what can be improved - I'll be happy to hear.
Comments
Hello, a very nice project. What are the gears of the guitar taken from? Now, if you have a lathe, you can make a better spindle drive wheel hub, because the current assembly does not look the strongest. ... [Read more]
In the guitar, as well as in the support, standard 1.5 module gears (only the first stage of the feed, module 1) are available in online stores or Allegro. Contrary to appearances, the pulley holds up... [Read more]
Milled support sled, did you get it? [Read more]
A piece of good work, especially since it was made without the use of another lathe. Only a friend probably made a mistake in the order of magnitude and wrote that the spindle bore was 250mm :D The lack... [Read more]
As I wrote, no machine tools were used and, perhaps anticipating the next question - I did not believe it either, but I assure you - it is possible to make guides without a milling machine once, after... [Read more]
Cool design. Guitar shift wheels can be purchased. And the horse, knife holder, handle can also be bought? All in all, however, access to a milling machine would be desirable. [Read more]
Milling on the video from the link is quite practical, cool at eye level. I like your design. If I can ask you for a video of the rolling, it will show us a lot. Do you have any drawings with dimensions?... [Read more]
I will say that art for art - a steel, flexible bed does not provide any stiffness in fact. The cost of implementation certainly exceeded the value of even TSB16, with a fraction of the functionality of... [Read more]
Congratulations on your patience, it's a really good job for an amateur lathe. Write down how you made "circles" pointers to measure. You punched or milled the numbers. [Read more]
Not cool at all, because such a thin shield can break and ricochet in the face. Generally, these are sick ideas, because grinding is great (that's what it is called), but with a thick disc, e.g. 10mm,... [Read more]
It was a sarcasm. Sick, little to say. [Read more]
Crap, scraping with a good gauge can be more thorough than grinding. It's all a matter of time and skill. In this case, in addition, the stiffness of the bed. I'm just worried about wiping the... [Read more]
Looking at your TSB16 and your something - I admire it - a bottom bracket like in the TSB16 - and the rest with a pinch of salt similar. [Read more]
Hello, I have comments on the electrical system of the lathe. According to the instructions for the inverter used here (link to pdf: www.zeltech.pl/download-file/201204/Instruction%20SJ100%20poło.pdf)... [Read more]
Roll the cones like you can't - how you can :D here 60 ° https://obrazki.elektroda.pl/2972286700_1513952442_thumb.jpg https://obrazki.elektroda.pl/1017666200_1513952445_thumb.jpg https://obrazki.elektroda.pl/3028394600_1513952446_thumb.jpg... [Read more]
I recommend tossing the rods into vinegar for a few hours before processing. The rust is quite hard and destroys knives, not to mention the powdered one makes a mess on the lathe. [Read more]
The only thing I can fault is a badly mounted item at the end of the video. The post screws, are they the usual M8? Why allen heads? [Read more]
Such an ordinary M8 and for which hexagonal ones - the most convenient for me, you will not buy the original for a post with square heads just like that. As for the attachment of the last shaft - only... [Read more]
With the Allen ones the head is quickly damaged. You already have a lathe, now you will cut such a "square" screw (: Have you measured the clock on the handle? I am asking out of curiosity what you... [Read more]