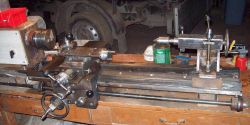
I was wondering if this design fits in this forum, but I can see that they were already similar, so it will be a bit of a change in this section.
Often I was faced with the problem of rolling a shaft (bushings, washers), and anyone who made extra money using the method: a drill mounted in a vice and a file or an angle grinder knows what the "torture path" is, not to mention the limitations of such a method.
Honestly, I initially wanted to buy a table lathe (ie TSB16), but practically all of them would be - as agreed, all of them were at the other end of Poland, and if it gets closer, the price is unacceptable.
So I decided to build from scratch, as is well known - you need a lathe to build a lathe but in my case this is not the case, for the construction I used only the hand tools available in almost every workshop.
Initially, I planned to make the spindle itself with a lathe chuck, so that the material could be processed with a file or grinder, then I tried to use a cross vise (which I had) as a support, the result - a failure.
Finally, I made a bed and a support from scratch, and then I could add new elements on it: gear, feed, tailstock.
DESCRIPTION:
Spindle - shaft on 2 tapered roller bearings, unfortunately not a through hole (I had one), but inside a 250mm fi25 hole.
Drive: 3-phase 0.55kW motor powered by an inverter and a single-stage gear with a ratio of approx. 1 / 2.6.
Bed - angle 120.
Lead screw - Tr20x4, cross slide and tailstock - Tr14x4 left-handed, tool sled - Tr12x3.
The bolts of the cross slide and the carriage are supported on both sides by thrust ball bearings, the lead screw from the right has 2 tapered bearings to eliminate the longitudinal play.
Longitudinal support - on the crank gear 17z to 34z and together with it 17z with a toothed rack module 1.5, which results in: 1 turn of the handle = 40.055mm.
The rest in the photo:
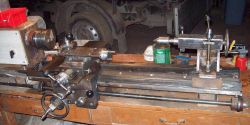
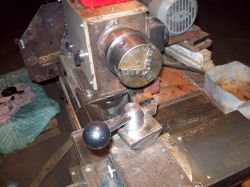
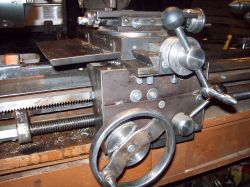
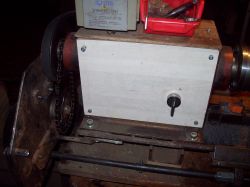
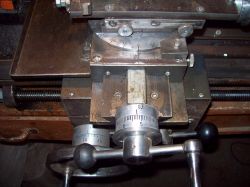

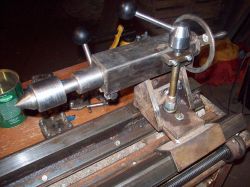
Here the guitar, gear spindle-intermediate shaft 1/2 chain, then toothed gear: two-stage for feed, and one-stage for threads (all pitches of metric threads can be obtained with one gear), for the 3rd photo setting for a pitch of 1 mm 14z / 28z plus the switch, i.e. left-hand thread in this case.
In the last photo, the larger threads are a typical M10, and the smaller one is M8x1 left.
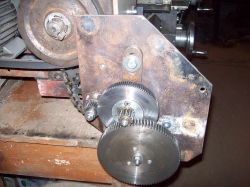
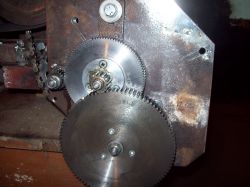
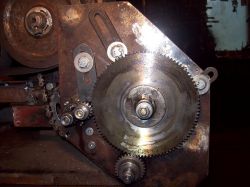
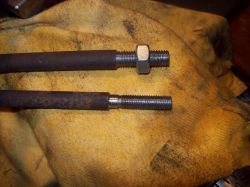
Rod fi 20 knife with plate and HSS
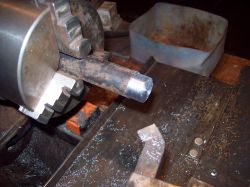
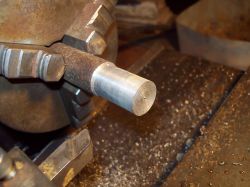
I know that it cannot be compared to the factory design, but not too large elements can be successfully re-threaded, the feeds are two (replacement of the gear on the intermediate shaft) with the diameter of the material, say fi 25 - max. thickness per one pass is about 0.6..0.7mm - with a feed rate of 0.05mm / rev.
Maybe someone has built similar devices and will share suggestions on what can be improved - I'll be happy to hear.
Cool? Ranking DIY