Hello
I am looking for a diagram or at least information on what regulates the 3.3 V voltage supplying the main circuits in the Thrustmaster TX steering wheel board.
The board has a 24V power supply (mainly for motor power), which is activated when the USB cable is connected (by sending 5V to the power supply).
I found one DC-DC regulator (TPS54040) on the board, which reduces the voltage to 12 V to power the cooling fan. I suspect that from the same 24V line, or from the mentioned 12V, the voltage is reduced to 3.3V, but I have no idea where. Have any of you had any experience with this board?
Currently, after connecting the USB to the computer, the voltage on the systems slowly increases to 0.4 V. I don't think so. that 3.3V is obtained from 5V from USB - a friend who has a working T500RS (very similar in construction) - when connecting only USB without the power supply, the steering wheel is not even detected.
I connected an external 3.3 V power supply to one of the capacitors of the power supply line (the one in the orange frame in the picture) and the steering wheel came to life - the PC detected it correctly, the motor turned a little, so the control should also be ok. The steering wheel was detected, I even managed to update the firmware but the steering wheel position sensor (AS5048A) and none of the buttons work. The 3.3 V that I connected also reaches the sensor and is consistent with its data sheet.
I wonder if such an external power connection does not cause another problem that makes the signals not detected by the main cube. So I wanted to start by fixing the 3.3V power supply.
The board itself is based on the TM4C123GE6PZ cube, plus the DRV8301 brushless motor driver - both powered from 3.3 V.
There is one chip that I can't identify - on the housing there is something like this: 35901 74203 he327 and it has 10 pins - do you know what it could be?
Pictures below, thanks in advance for your help.
I am looking for a diagram or at least information on what regulates the 3.3 V voltage supplying the main circuits in the Thrustmaster TX steering wheel board.
The board has a 24V power supply (mainly for motor power), which is activated when the USB cable is connected (by sending 5V to the power supply).
I found one DC-DC regulator (TPS54040) on the board, which reduces the voltage to 12 V to power the cooling fan. I suspect that from the same 24V line, or from the mentioned 12V, the voltage is reduced to 3.3V, but I have no idea where. Have any of you had any experience with this board?
Currently, after connecting the USB to the computer, the voltage on the systems slowly increases to 0.4 V. I don't think so. that 3.3V is obtained from 5V from USB - a friend who has a working T500RS (very similar in construction) - when connecting only USB without the power supply, the steering wheel is not even detected.
I connected an external 3.3 V power supply to one of the capacitors of the power supply line (the one in the orange frame in the picture) and the steering wheel came to life - the PC detected it correctly, the motor turned a little, so the control should also be ok. The steering wheel was detected, I even managed to update the firmware but the steering wheel position sensor (AS5048A) and none of the buttons work. The 3.3 V that I connected also reaches the sensor and is consistent with its data sheet.
I wonder if such an external power connection does not cause another problem that makes the signals not detected by the main cube. So I wanted to start by fixing the 3.3V power supply.
The board itself is based on the TM4C123GE6PZ cube, plus the DRV8301 brushless motor driver - both powered from 3.3 V.
There is one chip that I can't identify - on the housing there is something like this: 35901 74203 he327 and it has 10 pins - do you know what it could be?
Pictures below, thanks in advance for your help.
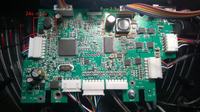
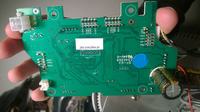