
I will present here a unique set of universal boards for SMT microcontrollers in cases like TQFP100, TQFP64 and TQFP48, various SSOP, SOIC, etc. filters, power block) and a large amount of free space for additional systems (prototyping zone).
As part of the demonstration, I will setup a basic breakout for different microcontrollers, two made by Microchip and one by Silabs. In addition, I will present a few examples of peripherals for one of these microcontrollers, including EEPROM to I2C, USB to UART converter, ADC and a potentiometer, all to show how conveniently you can place the necessary elements and solder to the boards presented here.
Jon Newcomb universal SMD breakout boards
I got these plates as samples from Jon Newcomb to show them to the Electroda users. The boards can be purchased on the website below:
https://www.ebay.com/usr/jon_newcomb?ul_noapp=true
I also invite you to the author's website: http://www.jnewcomb.com
Here are the available versions of the boards:
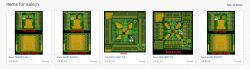
Promotional graphics, on the example of the TQFP100 version:
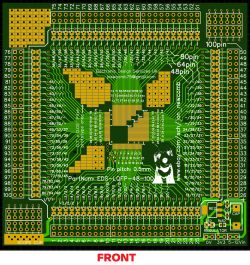

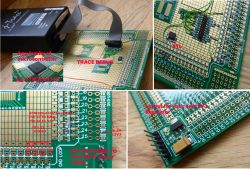


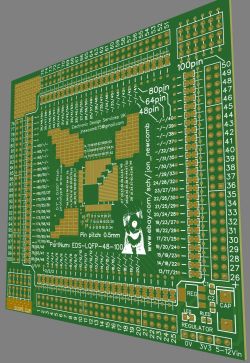
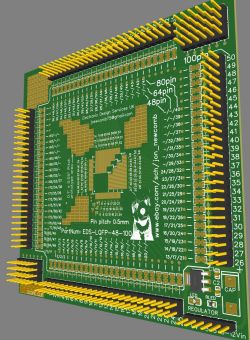


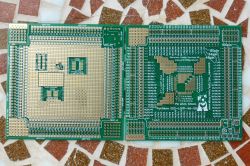
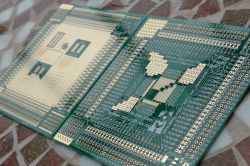

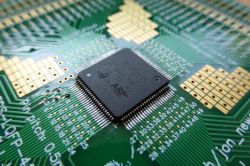
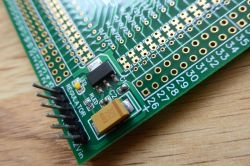
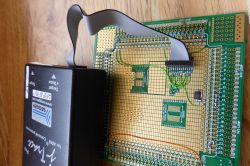
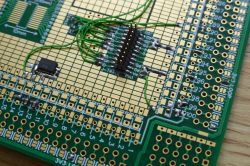
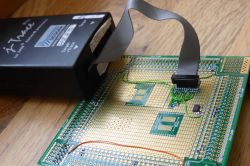
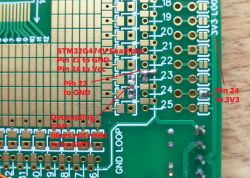

Versions are available:
- VSSOP8, VSSOP10, VSSOP20, SSOP28, SOT-353 panel
- QFP LQFP TQFP 48,64,100pin 0.5mm
- set of 4 - SOIC24 SOIC-24 (0.05 ", 50mil, 1.26mm)
- set of 2 - LQFP QFP TQFP QFN MLF 32/48 pin 0.5mm
- set of 4 - SSOP24 0.635mm TSSOP MSOP
- set of 4 - VSOP VSSOP MSOP QSOP MSSOP 0.5mm
- a set of 4 pieces - SSOP SSOP24 0.65mm
These boards are distinguished by the fact that they have paths so that the power and ground connections to various pins are basically ready, all you need to do is put a tin jumper.
Let's look at the TQFP 100 for example:
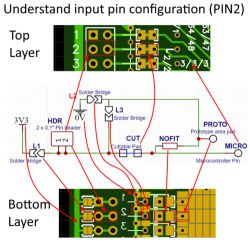
Thanks to this, there are no problems with:
- connecting the pin to ground
- connecting the pin to the power supply
- connecting a capacitor between the pin and ground or between the power supply and ground (for example VCAP from PICs)
- connecting a filter on the pin input (e.g. analog, AVDD)
- connecting a pull-up resistor for the pin
- etc. etc.
In addition, they offer ready places for the power section, programmer outputs and a large field for prototyping. The prototype fields are made in a thoughtful way, and in some boards (eg TQFP100) they also include pads for smaller chips in SOIC and SSOP. There is also room for the ETM-TRACE debugger in the TQFP.
An additional example of the universality of jumpers
But it is not everything. After re-examining the picture:
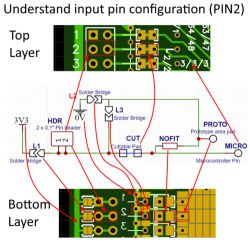
you can even think of a way to conveniently connect the LED with a resistor on the GPIO of the microcontroller.
1. Cross the "cuttable pad" from the diagram
2. We solder the LED in its place
3. We bridge L3
4A. (if we want to ground) L3 is bridged, on L2 we solder the SMD resistor (say 330 ohms in 0805 housing) or axial on L2 / L3 pads with vias
4B. (if we want to supply power) We solder the resistor on L1
Ready! LED in place, no unnecessary wires and combinations.
The kit I received
Let's start with how the tiles look in practice. The first set I received:

This large TQFP100 board is the same three times in the picture, there is just a large prototype space on the bottom and descriptions of the role of the pins on the top, etc. their derivation.
The second set I got - 48 / 32pin 0.5mm QFP QFN:
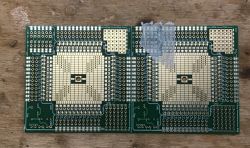
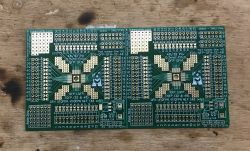
At first glance, you can see that the tiles are of very good quality, but we will test them in practice anyway.
Soldering equipment used
For the demonstration of the board, I will use the most problematic soldering iron I have, i.e. a soldering iron, the tip of which I have not replaced since its purchase, additionally without power regulation.
This is to demonstrate that you don't really need super hardware to run some microcontroller on these boards.
Additionally, you have to forgive me for the poor quality of the solders, but I can see quite poorly and physically I am also not a master of coordination of movements.
Here is my soldering kit used for this topic:
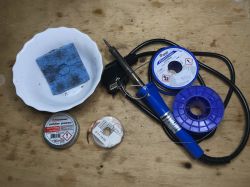
We have here:
- 30W silverline soldering iron
- a sponge for cleaning the tip (I also have an ammonium chloride)
- Sn60Pb40 solder binder (lead) in two versions, 1mm for THT and 0.25mm for SMD. I choose them because of their low melting point (lead-free to have a higher melting point)
- soldering paste (how to make a bridge on the TQFP pins, then a bit of paste + movement along the pins / paths with the tip may save the situation)
- braid for removing excess binder, including removing bridges on SMD pins as the paste method will fail
In addition, I also have an IPA agent to remove the flux after soldering from the board. That's it - no soldering stations, no hot air, no temperature controls ... nothing like that. A beginner can easily run the TQFP-100 chip without such frills.
TQFP 100 Demonstration - PIC32MZ2048EFG100
It's time to demonstrate the use of this tile in practice.
We will run PIC32MZ2048EFG100 on it - 32-bit microcontroller with 2MB flash memory and 512KB RAM.
NOTE: There are different types of TQFP 100 - some have 0.4mm pin spacing, others 0.5mm. The 0.4mm version will not fit this board ... the 0.4mm version is called PIC32MZ2048EFG100-E / PT and the 0.5mm version is called PIC32MZ2048EFG100-I / PF.
Anyway, everything is in his catalog note. We will need it:

You also need information about the findings:
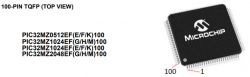
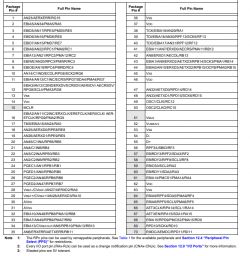
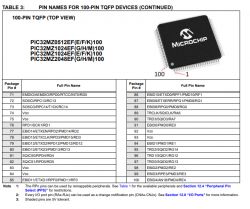
ATTENTION: Pin number 1 is the pin at the corner with a dot. The orientation of the text / graphics on the layout does not matter. It can sometimes be reversed. Adopting it may be misleading.
Additionally, let's check what needs to be connected - section 2.1 Basic Connection Requirements :
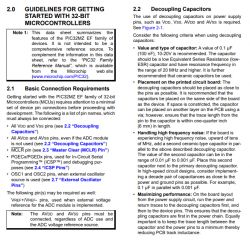
We will stretch the rules a bit here, because decoupling capacitors should be " placed as close to pins as possible "(placed as close to the pins as possible) to minimize parasitic capacitance and inductance, and here is a bit of this gap, but I think it's acceptable for a learning breadboard.
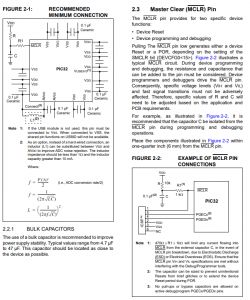
Basically we have to do:
- soldering the circuit to the board
- jumpers for all VDD and GND pins (also AVDD and AGND)
- decoupling capacitors 100nF for pins from the power supply
- connection of the Pickit programmer via ICSP on MCLR / VDD / GND / PGD / PGC
- LDO 3.3V with 5V input from USB (PIC32MZ requires 3.3V)
Let's start by soldering the PIC. Positioning the system, I do it with antistatic tweezers but I do not touch its pins anyway, so as not to damage it with ESD, only the housing:
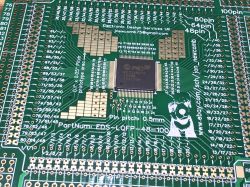
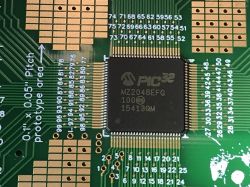
Pin catching, I use 0.25mm lead tin, must also be flux:
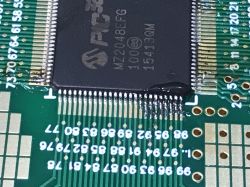
Soldering; there were practically no short-circuits on the pins (but when there is a short-circuit, first I try to remove them with the soldering iron + paste, with movements along the pins, and if it does not go with a braid):
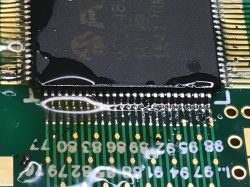
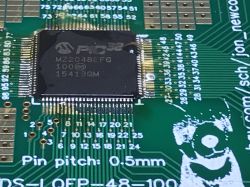
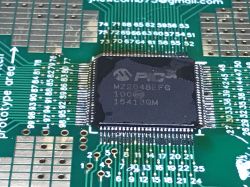
After soldering, each pin must be checked, both for connection and for a short circuit with neighbors:
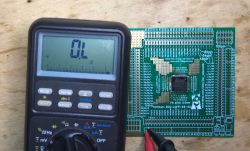
Now all the VDD and GND pins need to be soldered.
We have a download for this:
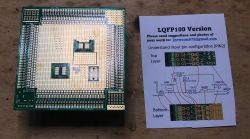
Pin 14 is the power supply. Below is a jumper for VDD loop:
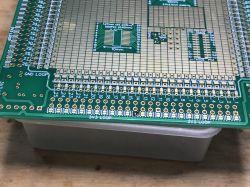
Pin 13 is ground. Below the jumper to GND loop:
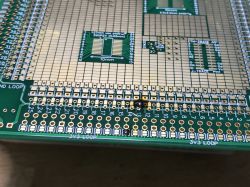
After each jumper, we check whether we have made a short circuit to the power supply (or to the adjacent pins), because then when there is a short circuit, it will be more difficult to determine when it arose!
Ready:

Now we will do the power section.
You will need LDO - AMS 1117:


Unfortunately I didn't have it in stock (I always use TC1264, MIC2940, etc). I had to find mine in the hatch:
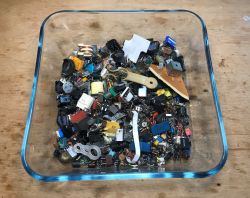
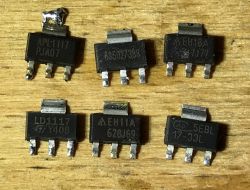
I chose the 5EBL17-33. We can set it first and then solder it, and you can also first put the tin on one pad and then position it, while melting the tin:


In the meantime, you can also solder goldpins from the power supply:
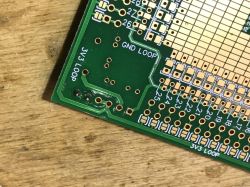
Ready. Now let's prepare 100nF ceramic capacitors in 0603 housing. In total, one is already in the picture below - see?
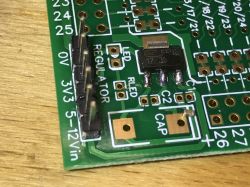
They have no polarity.

I solder them so that I tin one pad like this:
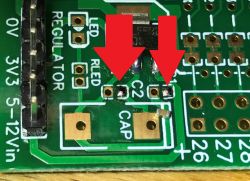
I position the capacitor by melting the binder on that pad, then solder the other contact:
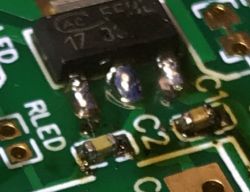
Now it's time for the electrolytic capacitor. Those in SMD have a line where their + is. The capacitors at LDO are not just for show, they are necessary for its proper operation. I had to find my capacitor in the outlet:

Here, too, it may be more convenient to whiten one pad first, then warm it up, place the element, and then solder the other contact.


Now decoupling capacitors for the VDD / GND pin pairs. Also at 100nF, such as before:
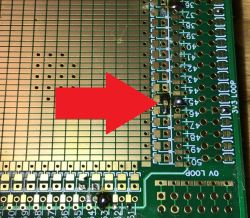
The same for every couple.
Next in line is the programming connector, six-pin (basically a five-pin one is enough). The tile is so thought out that there is even a good place for it:
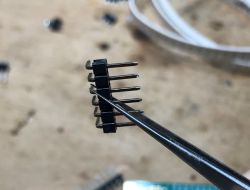

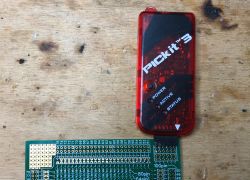
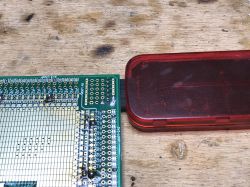
I led the angular ICSP pins with the wires to the double goldpin strips, first these strips also had to be soldered:
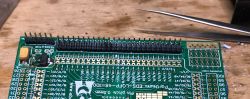
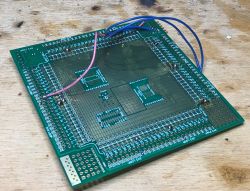
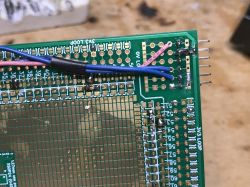
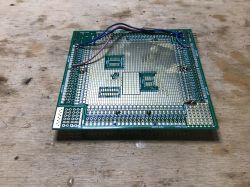
Time for a USB connector. It will make it easier to connect the 5V power supply to the input of the already installed 3.3V LDO:
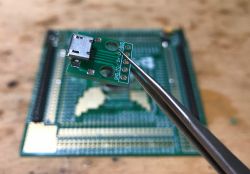

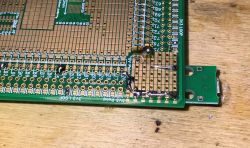
The mass is easy to connect, 5V must be connected to the LDO by a cable:
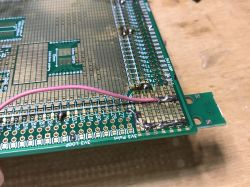

The 10k resistor between MCLR and VDD has also been soldered (pull-up, forces the high state on the resetting pin):
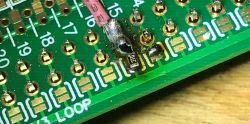
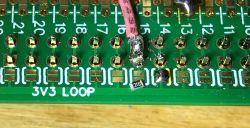
(this cable goes from the ICSP connector to the MCLR, it's not the power supply).
Basically that's it, all that's left to do is get the rest of the pins out. I decided to add one more LED, of course, with a resistor (also in the 0603 housing), with the goldpin output, so that I could connect it to any other pin with a female-female cable.
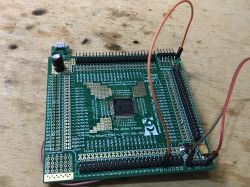
PICKIT3 already allows you to program the PIC:
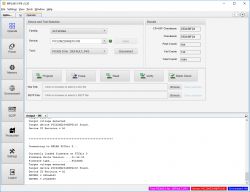
You can upload blink led:
Code: C / C++
The system works and the LED flashes, even when powered by a powerbank (flashlight):

Additives for PIC
These boards, however, allow much more than just starting a microcontroller.
You can also easily solder additional integrated circuits, e.g. the MCP2221 USB to UART converter:
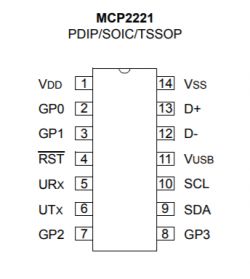
I chose the MCP2221 over the MCP2200 as the latter would require an external quartz resonator.
The MCP2221 itself does not have big requirements:
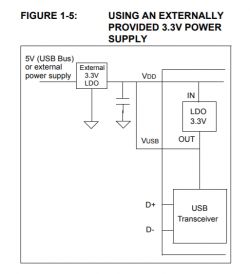
In addition, a 10k resistor on the RST pin (pull up), of course a 100nF capacitor for the power supply ...
There is a place on the board just in time for this layout:
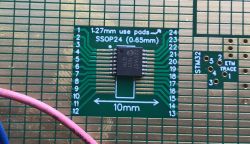
We solder:
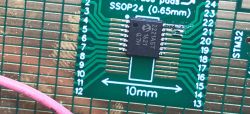
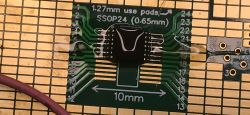
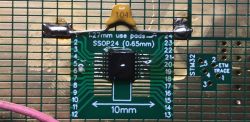
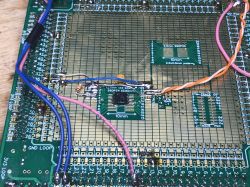
I led RX / TX to these goldpins to be able to freely decide which PIC pins I will connect to MCP2221:
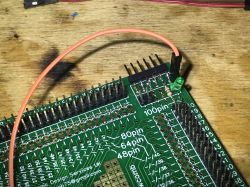
Still need a test program ... you need to use PPS (Peripheral Pin Select) to select a pin to assign the role of TX output.
Code: C / C++
UART works!
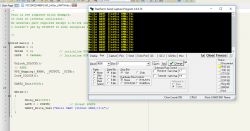
Now we solder 24AA256, which is 256KBit EEPROM memory with I2C interface:

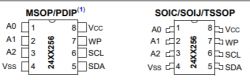
Pins defining the address (A0, A1, A2) I will short circuit to ground for convenience. The WP status must also be low to disable the write lock.
PIC32MZ has no I2C on PPS (Peripheral Pin Select), only on specific pins. But we have 5 different I2C modules to choose from. I chose I2C3:
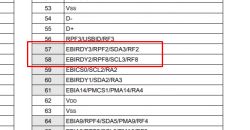
We solder:
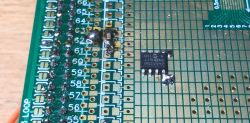
Capacitor 100nF:
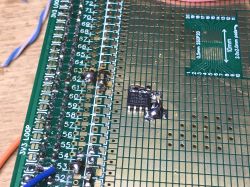
SDA / SCL lines to PIC:

More pull-up resistors for SDA / SCL lines:
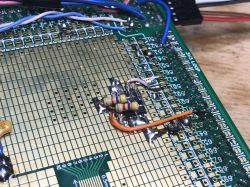
It's time to check communication (at least initially):
Code: C / C++
The PIC sees the I2C device with the address 160:
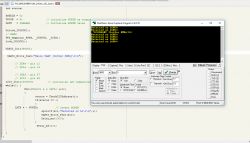
Now maybe something more banal. Potentiometer, for ADC presentation. In the case of this board, there is a place for it, we solder it like we soldered the RESET button.
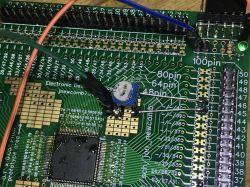
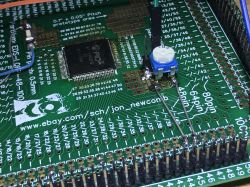
These connections to pins 45/46 are of course ground and power connections. I put the potentiometer between the ground and the power supply, and its tap is the output of the voltage divider, and the ADC reads this voltage from it.
Code:
Code: C / C++
Result:
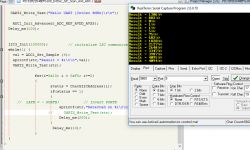
The potentiometer works, as you can see on this PCB, you can do even quite a large project, and the prototype spot on top is also useful.
TQFP48 Demonstration - EFM32ZG222F32
Now it's time to present the second board based on a 32-bit Silabs microcontroller with the ARM Cortex-M0 + core:
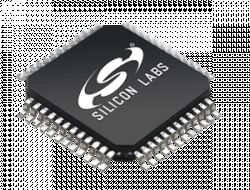
Here, however, everything is the same as on the TQFP-100 version, so the commentary will be shorter.
Here we also rely on the catalog note of the layout:
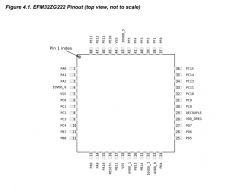
The note must be read carefully - you must not forget, for example, about the necessary Decouple capacitor (in PICs it is called Vcap or Vusb):

We start soldering.
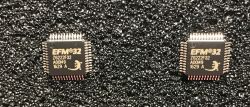
Positioning:
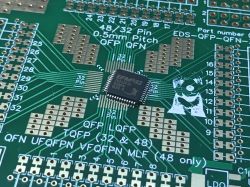
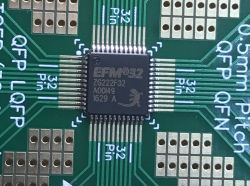
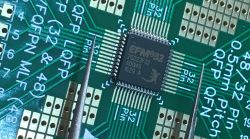
Here I tried to catch the chip with flux:

Soldering:


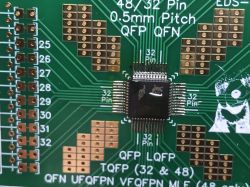
Power block. AMS1117. A bit of binder for the first pad ...
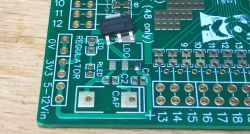
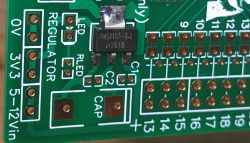
Jumpers from GND and VDD Loop:
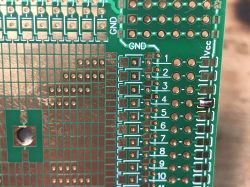
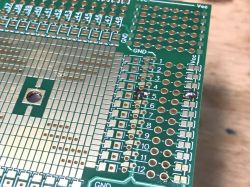
DECOUPLE pin. A capacitor with a Cdecouple capacity, i.e. 1uF.
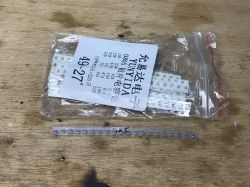
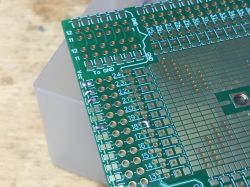
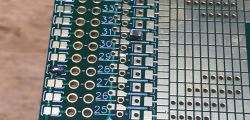
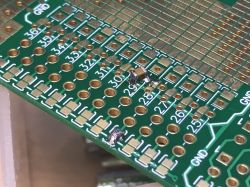
Double rows of goldpins:

100nF capacitors on input and output AMS1117:
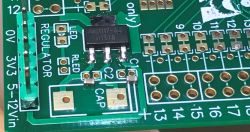
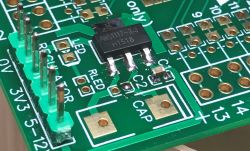

4.7uF capacitor, also from the outlet:
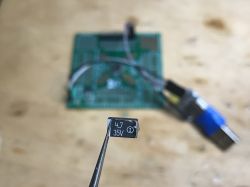
Binder on the pad:
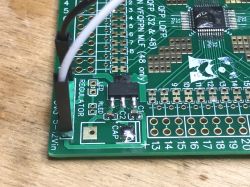
Soldered:
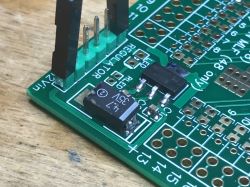

Ready chip for bootloader test:
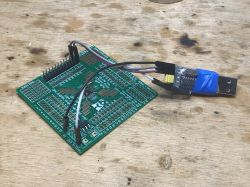
The bootloader responds to the "U" character, i.e. EFM running:
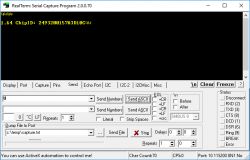
I do not have the environment and compiler prepared for this system. In case of additional progress, I will complete the topic.
Of course, this is how you can also run other microcontrollers ...
For example, such ATSAMD21G18. I also started a trial with it, however it is not complete as my programmer for it is still on its way.
This time just a few pics - everything as before.



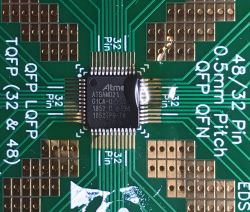

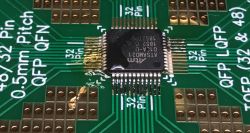
If I manage to start it, maybe I will do an ATSAM project on this board and also publish it on the forum.
SOIC24 demonstration - what if we have a layout in SOIC28?
You can really carve a lot on these tiles. Now I will present a SOIC24 board (pitch = 1.26mm) using PIC32MX150F128B in SOIC28.
Yes, four pins will "hang" in the air, but thanks to the creativity of the tile's author, you can use them anyway:
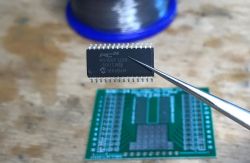
Pinout:
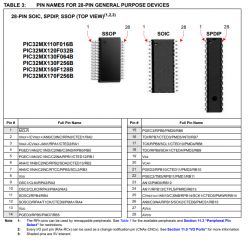
Connection required:
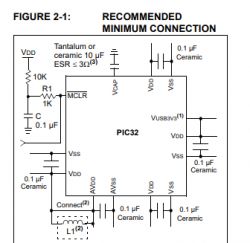

First pin soldered:
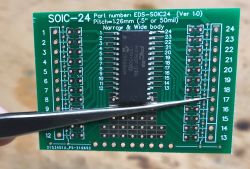
Next:

Bending the extra-number pins (a simple trick to use the SOIC24 to SOIC28 plate). After soldering:
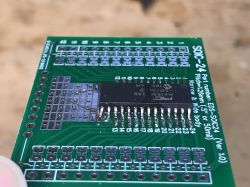
Jumpers for ground on the bottom (no power loop here, we'll do it manually):

VCAP capacitor (10uF, preferably tantalum, ESR
Cool? Ranking DIY Helpful post? Buy me a coffee.