Some time ago I bought 2 induction converters in China, hoping that despite the simple-looking structure and a really small number of elements, it will be possible to use this device in a workshop, e.g. as an aid in unscrewing stuck screws or, for example, in the process of hardening small metals. 120W of power is unfortunately very little for this type of construction, but the device is really decent.
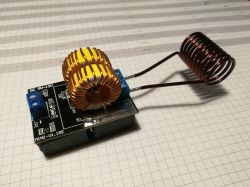
You can see at first glance that the number of elements is limited to the necessary minimum. The system consists of two mosfet transistors, two fast diodes, two inductances, resistors and resonant elements, i.e. an external coil and high capacity. During the first attempts, and basically when squeezing "as much as possible", I managed to damage the circuit, the transistors burned out. At first I inserted the IRFR120, but due to the low maximum current, they lasted only a moment. Then I soldered the IRFR2905 - 50A low voltage transistors, which seem to be appropriate - the heater works better than on the original mosfets, the marking of which is unfortunately not visible. The photos show a burning transistor.
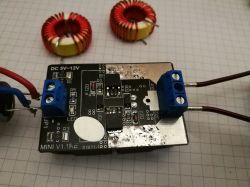
Let's move on to the tests.
After connecting the 12V DC voltage, the device consumes about 1.8A. As soon as the metal element is brought closer to the coil, the current begins to increase. At its peak, I managed to achieve a current of about 12A, which gives almost 150W, which is more than the manufacturer declares. During the idle run, despite the power consumption of about 20W, nothing heats up, rather a little bit of everything, which may prove the correct operation of the entire structure. At first, I connected the device to a universal power supply, which in its design has several taps on the transformer and relays that activate the appropriate voltage. Unfortunately - the heater most likely generates large disturbances that destabilize the operation of such a power supply, causing its chaotic switching. I built a simple transformer power supply quickly in order to be able to further test the device.
I tested three elements: a 6.5mm screwdriver, a figure-eight screw, and the same screw with two nuts. All three cases can occur in reality, so let's check how our heater will meet the set bar.
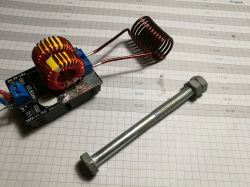
Screwdriver:
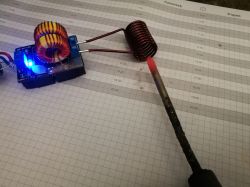
As you can see, a medium-sized screwdriver can be heated to redness with this device within 2 minutes. This is a pretty decent result in my opinion. If we can harden the tip of a screwdriver at home, then such a heater will be a great help here!
Eight screw:
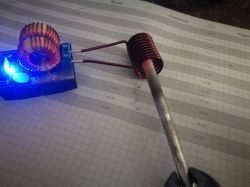
It takes about 3 minutes to make this screw red hot - it also seems to be a good result, of course considering the simplicity of the device. Also in this case, we can use this device to harden to a diameter of 8mm.
Bolt with nuts:
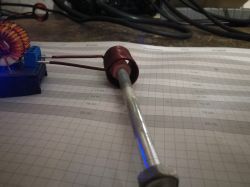
In this case, it took 4 minutes to warm up such a kit to a barely visible redness - a long time. The device under test can be used in this way to heat the baked cap in order to unscrew it easier, but the process will be long and inconvenient. In addition, in our case, we could put the heated elements inside the coil - in the real case it may not be possible, which will significantly reduce the efficiency of such an operation.
Summarizing...
one piece of "induction heater" cost about $ 9, which is less than PLN 35. In my opinion, this is a low amount for a device that is able to heat efficiently with low power, but small metal objects. Of course, this heater cannot be compared to company equipment for a few thousand zlotys, but it is also not just a worthless gadget and it will work for home, hobby or even small workshop applications.
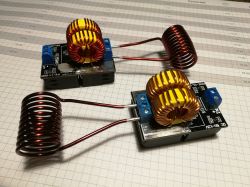
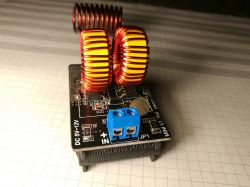
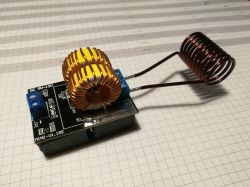
You can see at first glance that the number of elements is limited to the necessary minimum. The system consists of two mosfet transistors, two fast diodes, two inductances, resistors and resonant elements, i.e. an external coil and high capacity. During the first attempts, and basically when squeezing "as much as possible", I managed to damage the circuit, the transistors burned out. At first I inserted the IRFR120, but due to the low maximum current, they lasted only a moment. Then I soldered the IRFR2905 - 50A low voltage transistors, which seem to be appropriate - the heater works better than on the original mosfets, the marking of which is unfortunately not visible. The photos show a burning transistor.
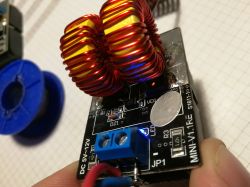
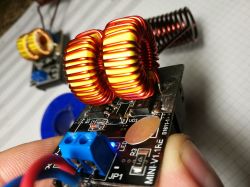
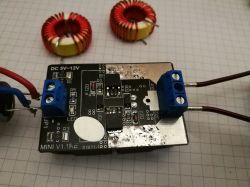
Let's move on to the tests.
After connecting the 12V DC voltage, the device consumes about 1.8A. As soon as the metal element is brought closer to the coil, the current begins to increase. At its peak, I managed to achieve a current of about 12A, which gives almost 150W, which is more than the manufacturer declares. During the idle run, despite the power consumption of about 20W, nothing heats up, rather a little bit of everything, which may prove the correct operation of the entire structure. At first, I connected the device to a universal power supply, which in its design has several taps on the transformer and relays that activate the appropriate voltage. Unfortunately - the heater most likely generates large disturbances that destabilize the operation of such a power supply, causing its chaotic switching. I built a simple transformer power supply quickly in order to be able to further test the device.
I tested three elements: a 6.5mm screwdriver, a figure-eight screw, and the same screw with two nuts. All three cases can occur in reality, so let's check how our heater will meet the set bar.
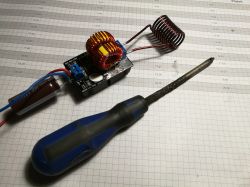
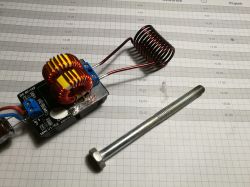
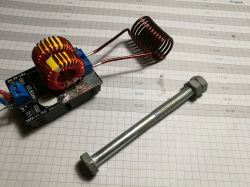
Screwdriver:
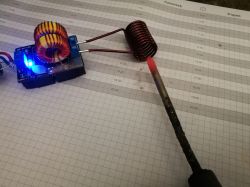
As you can see, a medium-sized screwdriver can be heated to redness with this device within 2 minutes. This is a pretty decent result in my opinion. If we can harden the tip of a screwdriver at home, then such a heater will be a great help here!
Eight screw:
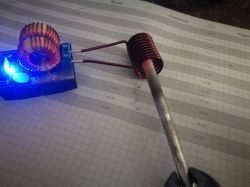
It takes about 3 minutes to make this screw red hot - it also seems to be a good result, of course considering the simplicity of the device. Also in this case, we can use this device to harden to a diameter of 8mm.
Bolt with nuts:
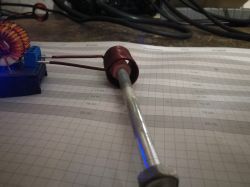
In this case, it took 4 minutes to warm up such a kit to a barely visible redness - a long time. The device under test can be used in this way to heat the baked cap in order to unscrew it easier, but the process will be long and inconvenient. In addition, in our case, we could put the heated elements inside the coil - in the real case it may not be possible, which will significantly reduce the efficiency of such an operation.
Summarizing...
one piece of "induction heater" cost about $ 9, which is less than PLN 35. In my opinion, this is a low amount for a device that is able to heat efficiently with low power, but small metal objects. Of course, this heater cannot be compared to company equipment for a few thousand zlotys, but it is also not just a worthless gadget and it will work for home, hobby or even small workshop applications.
Cool? Ranking DIY