Hello
I would like to present for evaluation, possibly to indicate errors and defects of my cell welding machine.
I do not have access to professional tools, so the housing looks like it looks. It is made of metal sheets left over from a microwave oven, the front part is made of plywood because of easier processing.
What should be changed in it:
- convert the cable from 25 mm2 to 35 mm2
- press the ring terminals with a hydraulic press
- replace aluminum elements with copper ones in the handle with electrodes
Initial parameters:
1300 W transformer
Secondary winding cross-section 25 mm2
The voltage of the secondary winding is 3.3 V
Short-circuit current on the secondary winding 750 A (the meter has a scale of up to 600 A)
The 40 A driver and electrodes were purchased on aliexpress.
Current parameters:
Secondary winding voltage 5V
Short circuit current on the secondary 910 A
A video showing the production of the welding machine:
Photos of the welding machine:
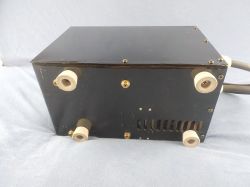
To make the handle of the welding machine, I used aluminum flat bars, dedicated welding electrodes, springs, screws, OSB and plastic.
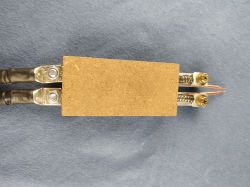
The inside of the welding machine
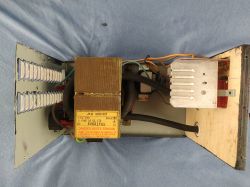
I temporarily insulated the side wall of the welding machine with paper (probably barley) before any contact with the controller.
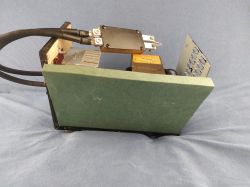
Update 9/11/2020.
Today I made modifications to the welding machine. The insulation was stripped from the 25 mm2 wire, instead I used two layers of Kapton tape and paper insulation (probably barley). Thanks to this, a few more turns came in and the voltage increased to 5 V.
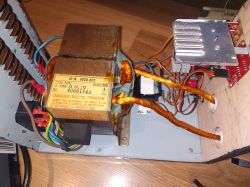
Update 10/11/2020.
I have assembled everything, the result is 910 A. All that is left to do is to make electrode handles and the project is completed.
I would like to present for evaluation, possibly to indicate errors and defects of my cell welding machine.
I do not have access to professional tools, so the housing looks like it looks. It is made of metal sheets left over from a microwave oven, the front part is made of plywood because of easier processing.
What should be changed in it:
- convert the cable from 25 mm2 to 35 mm2
- press the ring terminals with a hydraulic press
- replace aluminum elements with copper ones in the handle with electrodes
Initial parameters:
1300 W transformer
Secondary winding cross-section 25 mm2
The voltage of the secondary winding is 3.3 V
Short-circuit current on the secondary winding 750 A (the meter has a scale of up to 600 A)
The 40 A driver and electrodes were purchased on aliexpress.
Current parameters:
Secondary winding voltage 5V
Short circuit current on the secondary 910 A
A video showing the production of the welding machine:
Photos of the welding machine:
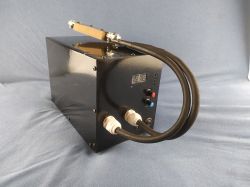
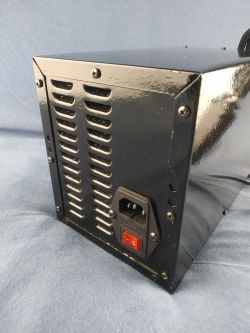
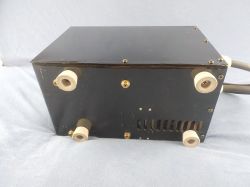
To make the handle of the welding machine, I used aluminum flat bars, dedicated welding electrodes, springs, screws, OSB and plastic.
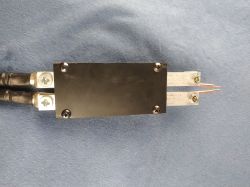
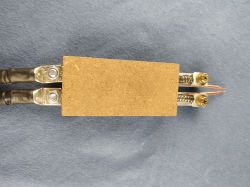
The inside of the welding machine
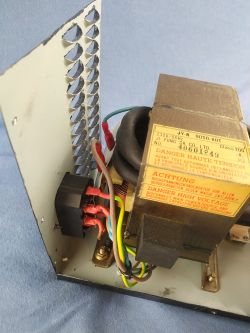
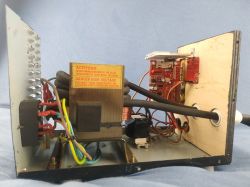
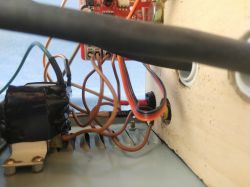
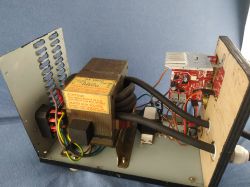
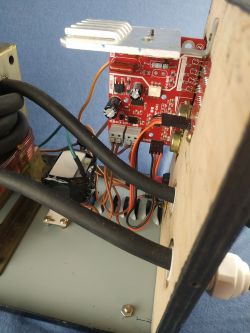
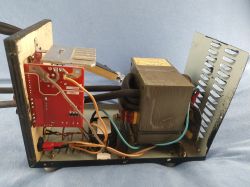
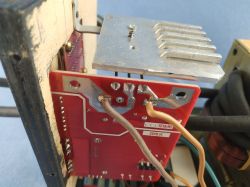
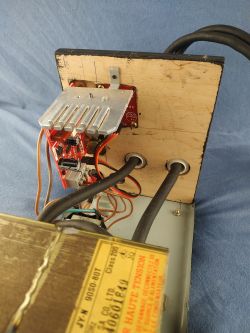
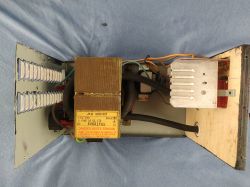
I temporarily insulated the side wall of the welding machine with paper (probably barley) before any contact with the controller.
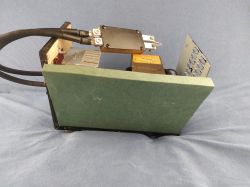
Update 9/11/2020.
Today I made modifications to the welding machine. The insulation was stripped from the 25 mm2 wire, instead I used two layers of Kapton tape and paper insulation (probably barley). Thanks to this, a few more turns came in and the voltage increased to 5 V.
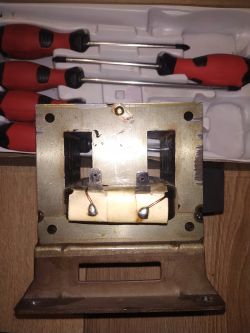
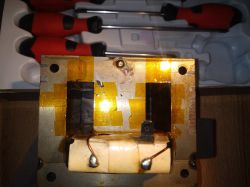
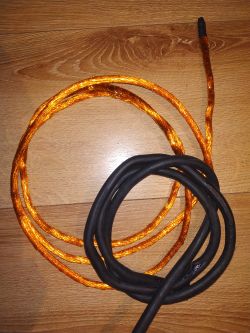
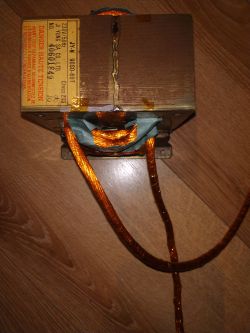
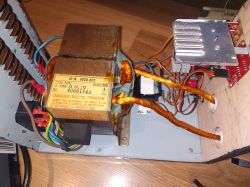
Update 10/11/2020.
I have assembled everything, the result is 910 A. All that is left to do is to make electrode handles and the project is completed.
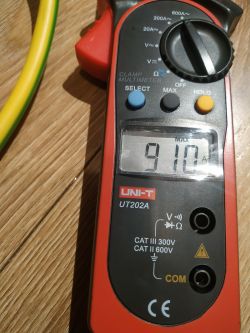
Cool? Ranking DIY