Hi.
Due to the fact that I would like to professionally deal with hardware design, I decided to work on a modest portfolio. I'm still learning Altium Designer, so I'm looking for interesting ideas to implement. In this case, it is also my first 4-layer board and I must say that from now on I will only make such
This is also the first board for which I ordered a SMD soldering screen. I must admit that with such a number of SMD components, the sieve is a great help.
As one project I plan to create in the future will have a high voltage component, I figured ST-LINK isolation might be useful. A few times, due to a small short circuit, I managed to kill the CPU, and I would not like my project to turn into a USB-KILLER at some point. :)
Insulation can be done in several ways. One of them is the isolation of the CLK and DATA signals of the SWD interface. After a short search, it turned out that this is not the optimal solution. For example, the ADuM1250/51 chip, which is an i2c bus isolator that could be used in this case, has a maximum speed limit of 1 MHz. SWD will work, but we will be forced to reduce the timing unnecessarily.
You can look for other, faster insulators, but this solution will still have several limitations.
So the natural choice seems to be to isolate the USB port itself. After a deeper thought, I found that once the programmer is connected, it would be good to have serial port options and connect a logic analyzer. Originally, I wanted to buy single, ready-made, passive USB 1.1 isolators from aliexpress, but I found that it would be more developmental to make something of my own. This is how the idea for the Isolated USB Hub was born. As an addition, I decided to add an isolated converter there, so that the hub was active. Initially, I was convinced that USB Full Speed would be sufficient, after all, such a device is quite specific and the transmission speed is not the main assumption here. It seems to me that around January there was no USB2.0 isolator on the mouser. It was also hard to find something in google, so the choice fell on:
- ISOUSB111DWEVM - USB Full Speed isolator. In version 0.2 changed to ADUM3166BRSZ - USB High Speed.
- USB2534I - HUB 4xUSB
- IES0205S05 - Isolated 5V/5V 2W converter for passive USB.
- LM5020 - Controller of the main DC/DC converter.
- TPS2552DBVT - USB port power controller with adjustable maximum output current
Let me discuss version 0.2 with some modifications that are imposed on the schematic and PCB version 0.3, which will be ordered perhaps in the near future.
The ADUM3166BRSZ chip is almost an application from the catalog note. The chip does not require any external resistors, everything is integrated and automatically configured in the chip itself. The secondary side of the circuit requires the connection of an isolated 5V voltage. Theoretically, there is a 3.3V linear stabilizer in the system, which can be used to power the U9 chip, but the experiments in version 0.1 showed that the current efficiency during start-up is not sufficient for stable operation (at least in the USB111 chip, to avoid surprises with the new chip and the new plate, I decided to use an external stabilizer right away). For proper operation, a 24 MHz quartz resonator and several filtering capacitors are also required.
The USB2534I is also not very complicated and basically its application is also a data sheet. Any configuration of the system consists in pulling up specific pins to power or ground. In my case all ports are set to ports that can charge batteries (BC_ENx) and boot with settings taken from internal eeprom (SCL/SDA). Hub activity pin and information about Full speed communication are connected to floor LEDs. The LED0 pin (activity) needs to be configured through the MPLAB Connect Configurator application, however, the application seems to have a problem with the appropriate drivers on Windows 10. I do not currently have a laptop with older Windows, so this option is not active. According to the catalog note, RBIAS must be 12 kΩ, a precision resistor close to the system is recommended.
The TPS2552DBVT chip is a USB port power controller. Port power is always on (Enable pin pulled to ground). Resistor R6 sets the maximum output current. If this current is exceeded, the Fault signal is shorted to ground, and a message appears in Windows that the voltage on the USB port is unstable. For a 210 kΩ resistor, the current limit is approx. 100 mA. When 5 V voltage appears from the main DC/DC converter, a 66 kΩ resistor is additionally connected, thanks to which the maximum current is increased to approx. 550 mA. On each power line there is a 120 µF capacitor, in accordance with the USB 8 specification. A capacitor and a resistor at the USB port may or may not be installed - depending on the issue of grounding from the host side. In my case, these elements are not soldered.
The IES0205S05 is an isolated 5V/5V 2W converter that powers the ports, isolator and hub in passive mode. In principle, I wanted each port to be limited to 100 mA (which would theoretically be too much with the maximum power consumption from all ports). Theory is theory, practice has shown that the resistor limiting the output current, 210 kΩ, is a bit too big and connecting even a regular flash drive turns off the power and the message about "unstable power" appears in Windows. In the end, the resistance value was fixed at 150 kΩ (so the output current is about 180 mA). In the case of a maximum load of 2 ports, the voltage drop on the USB is so significant that the message will appear anyway and the power supply voltage is cut off from the port. So, of course, when using passive mode, you have to be careful, but in case of overload, nothing is damaged. Higher current draw = voltage drop = load cut by TPS2522.
D5 and Q2 are power supply switching between active and passive - in case 5 V is lower than 5 V DC/DC, the latter is completely cut off with the Q2 mosfet when external power is connected.
The LM5020 is the main flyback controller. The transformer used is POE13F-50LD. The output voltage is 5 V, the maximum current with 2 windings connected to each other is 2.5 A. The converter has overcurrent protection in the form of voltage measurement on resistors R41 and R42. There is a small error in the current scheme and laminate. The point between the resistors R30 and R31 is not connected to each other, and the diagram lacks a connection between them and C20. Anyway, a simple modification in the form of removing all components and soldering in a 1 µF capacitor activates the internal LDO regulator, which is used to control the gate of the transistor.
The output voltage of the converter was set to 5.3 V to compensate for the voltage drop appearing on the diode D5.
A bit of a question arises whether an isolated converter is needed, after all, any charger can be used. Yes, there is a possibility that the PC and the HUB will have the same 24V power supply, but then isolation on the hub board is required.
The board is made to fit the 546-1455L801RD case from Mouser. I chose red and black, so the hub can also be called a gaming hub
All holes are handcrafted using a bench drill and files. It didn't turn out perfect, but I'm happy with it. Some descriptions and a logo are missing, maybe someday I'll do something with a thermal transfer. For now, I'll leave it as is
The board fits without any problems into the housing, it has a bit of slack that can be compensated with any foam. If it so happens that I will make version 0.3, the PCB will be extended by 3 mm so that it fits "in contact".
In the attachments I leave diagrams and Gerber files, if anyone is interested in project files, please pm me.
Due to the fact that I would like to professionally deal with hardware design, I decided to work on a modest portfolio. I'm still learning Altium Designer, so I'm looking for interesting ideas to implement. In this case, it is also my first 4-layer board and I must say that from now on I will only make such

As one project I plan to create in the future will have a high voltage component, I figured ST-LINK isolation might be useful. A few times, due to a small short circuit, I managed to kill the CPU, and I would not like my project to turn into a USB-KILLER at some point. :)
Insulation can be done in several ways. One of them is the isolation of the CLK and DATA signals of the SWD interface. After a short search, it turned out that this is not the optimal solution. For example, the ADuM1250/51 chip, which is an i2c bus isolator that could be used in this case, has a maximum speed limit of 1 MHz. SWD will work, but we will be forced to reduce the timing unnecessarily.
You can look for other, faster insulators, but this solution will still have several limitations.
So the natural choice seems to be to isolate the USB port itself. After a deeper thought, I found that once the programmer is connected, it would be good to have serial port options and connect a logic analyzer. Originally, I wanted to buy single, ready-made, passive USB 1.1 isolators from aliexpress, but I found that it would be more developmental to make something of my own. This is how the idea for the Isolated USB Hub was born. As an addition, I decided to add an isolated converter there, so that the hub was active. Initially, I was convinced that USB Full Speed would be sufficient, after all, such a device is quite specific and the transmission speed is not the main assumption here. It seems to me that around January there was no USB2.0 isolator on the mouser. It was also hard to find something in google, so the choice fell on:
- ISOUSB111DWEVM - USB Full Speed isolator. In version 0.2 changed to ADUM3166BRSZ - USB High Speed.
- USB2534I - HUB 4xUSB
- IES0205S05 - Isolated 5V/5V 2W converter for passive USB.
- LM5020 - Controller of the main DC/DC converter.
- TPS2552DBVT - USB port power controller with adjustable maximum output current
Let me discuss version 0.2 with some modifications that are imposed on the schematic and PCB version 0.3, which will be ordered perhaps in the near future.
The ADUM3166BRSZ chip is almost an application from the catalog note. The chip does not require any external resistors, everything is integrated and automatically configured in the chip itself. The secondary side of the circuit requires the connection of an isolated 5V voltage. Theoretically, there is a 3.3V linear stabilizer in the system, which can be used to power the U9 chip, but the experiments in version 0.1 showed that the current efficiency during start-up is not sufficient for stable operation (at least in the USB111 chip, to avoid surprises with the new chip and the new plate, I decided to use an external stabilizer right away). For proper operation, a 24 MHz quartz resonator and several filtering capacitors are also required.
The USB2534I is also not very complicated and basically its application is also a data sheet. Any configuration of the system consists in pulling up specific pins to power or ground. In my case all ports are set to ports that can charge batteries (BC_ENx) and boot with settings taken from internal eeprom (SCL/SDA). Hub activity pin and information about Full speed communication are connected to floor LEDs. The LED0 pin (activity) needs to be configured through the MPLAB Connect Configurator application, however, the application seems to have a problem with the appropriate drivers on Windows 10. I do not currently have a laptop with older Windows, so this option is not active. According to the catalog note, RBIAS must be 12 kΩ, a precision resistor close to the system is recommended.
The TPS2552DBVT chip is a USB port power controller. Port power is always on (Enable pin pulled to ground). Resistor R6 sets the maximum output current. If this current is exceeded, the Fault signal is shorted to ground, and a message appears in Windows that the voltage on the USB port is unstable. For a 210 kΩ resistor, the current limit is approx. 100 mA. When 5 V voltage appears from the main DC/DC converter, a 66 kΩ resistor is additionally connected, thanks to which the maximum current is increased to approx. 550 mA. On each power line there is a 120 µF capacitor, in accordance with the USB 8 specification. A capacitor and a resistor at the USB port may or may not be installed - depending on the issue of grounding from the host side. In my case, these elements are not soldered.
The IES0205S05 is an isolated 5V/5V 2W converter that powers the ports, isolator and hub in passive mode. In principle, I wanted each port to be limited to 100 mA (which would theoretically be too much with the maximum power consumption from all ports). Theory is theory, practice has shown that the resistor limiting the output current, 210 kΩ, is a bit too big and connecting even a regular flash drive turns off the power and the message about "unstable power" appears in Windows. In the end, the resistance value was fixed at 150 kΩ (so the output current is about 180 mA). In the case of a maximum load of 2 ports, the voltage drop on the USB is so significant that the message will appear anyway and the power supply voltage is cut off from the port. So, of course, when using passive mode, you have to be careful, but in case of overload, nothing is damaged. Higher current draw = voltage drop = load cut by TPS2522.
D5 and Q2 are power supply switching between active and passive - in case 5 V is lower than 5 V DC/DC, the latter is completely cut off with the Q2 mosfet when external power is connected.
The LM5020 is the main flyback controller. The transformer used is POE13F-50LD. The output voltage is 5 V, the maximum current with 2 windings connected to each other is 2.5 A. The converter has overcurrent protection in the form of voltage measurement on resistors R41 and R42. There is a small error in the current scheme and laminate. The point between the resistors R30 and R31 is not connected to each other, and the diagram lacks a connection between them and C20. Anyway, a simple modification in the form of removing all components and soldering in a 1 µF capacitor activates the internal LDO regulator, which is used to control the gate of the transistor.
The output voltage of the converter was set to 5.3 V to compensate for the voltage drop appearing on the diode D5.
A bit of a question arises whether an isolated converter is needed, after all, any charger can be used. Yes, there is a possibility that the PC and the HUB will have the same 24V power supply, but then isolation on the hub board is required.
The board is made to fit the 546-1455L801RD case from Mouser. I chose red and black, so the hub can also be called a gaming hub


In the attachments I leave diagrams and Gerber files, if anyone is interested in project files, please pm me.
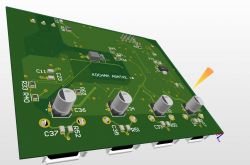
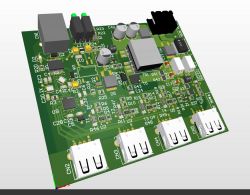
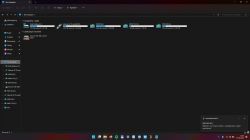
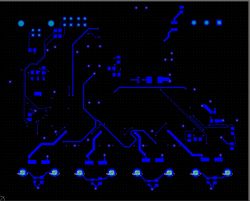
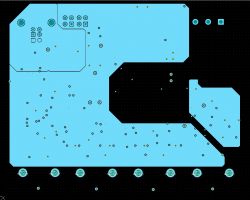
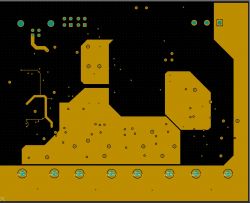
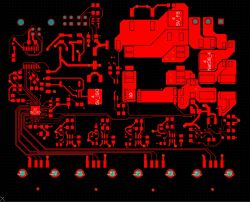
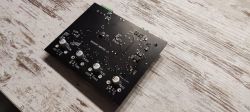
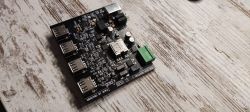
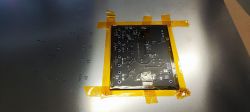
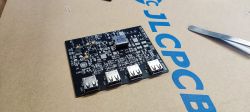
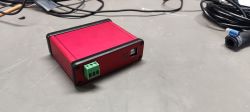
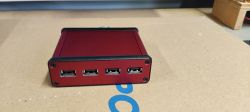

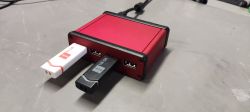
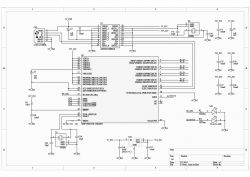
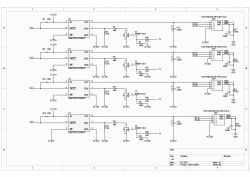
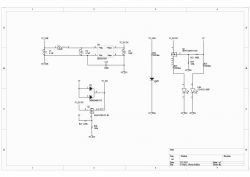
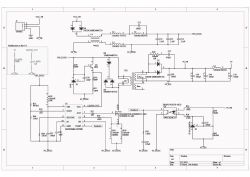
Cool? Ranking DIY