While I was doing a vise recently, I noticed that my cutting line was not straight. After putting two elements together, it turned out that there was a gap and then they had to be filled with a weld. So without thinking long, I decided that as soon as I finished the vice, I would start building a metal cutter.
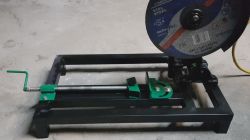
As the budget for this project was quite limited, instead of combining with an engine, septic tanks and belts, I decided to use an angle grinder, which was used once a year anyway. The grinder mounting was made of three pieces of a flat bar in which I drilled holes for the mounting screws. If necessary, the grinder can be dismantled by unscrewing three screws.
The arm is a rectangular profile with a 20mm diameter shaft, placed in two self-aligning bearings.
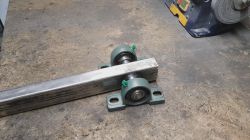
The top and legs are made of 30mm profiles.
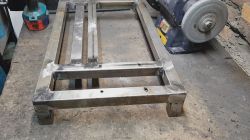
The support of the cut element is an angle that I carved for half a day to get a given shape.

The clamp is a piece of the profile shot through with a screw which was also shot with a piece of threaded rod.
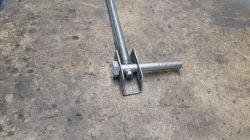
In order for the grinder not to fall, I used a gas cylinder found on the scrap metal.
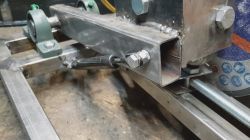
As for the costs, they are negligible.
Scrap profiles and flat bars PLN 1.50 per kilogram.
I had a 20mm shaft at home.
The self-aligning bearings lay in the shed.
So adding everything up did not exceed PLN 50.
To sum up, the project was successful and it meets my requirements, such as cutting at an angle of 90 and 45 degrees, which can be seen in the attached construction video. I'm waiting for opinions.
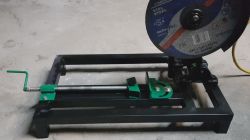
As the budget for this project was quite limited, instead of combining with an engine, septic tanks and belts, I decided to use an angle grinder, which was used once a year anyway. The grinder mounting was made of three pieces of a flat bar in which I drilled holes for the mounting screws. If necessary, the grinder can be dismantled by unscrewing three screws.
The arm is a rectangular profile with a 20mm diameter shaft, placed in two self-aligning bearings.
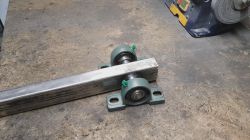
The top and legs are made of 30mm profiles.
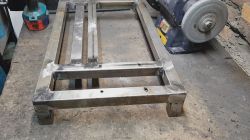
The support of the cut element is an angle that I carved for half a day to get a given shape.

The clamp is a piece of the profile shot through with a screw which was also shot with a piece of threaded rod.
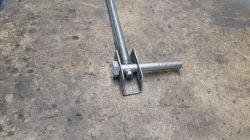
In order for the grinder not to fall, I used a gas cylinder found on the scrap metal.
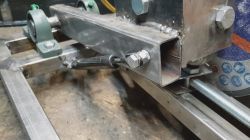
As for the costs, they are negligible.
Scrap profiles and flat bars PLN 1.50 per kilogram.
I had a 20mm shaft at home.
The self-aligning bearings lay in the shed.
So adding everything up did not exceed PLN 50.
To sum up, the project was successful and it meets my requirements, such as cutting at an angle of 90 and 45 degrees, which can be seen in the attached construction video. I'm waiting for opinions.
Cool? Ranking DIY