Good morning.
I wanted to introduce my next design which is a threading arm.
The base of the machine is a 400 kg magnetic lifter ordered from a well-known Chinese portal for the sum of 330 PLN.
.
I bolted a flat bar to the top of the magnet with a welded 30 mm shaft. I then screwed linear bearings to the 80x80 profile on both sides and put the whole thing on the shaft.
.
The next components of the arm are two 30x30 profiles which are supported by two 120 N actuators.
.
The last element of the arm is a screwdriver handle made of 15 mm sheet metal.
.
I also decided to make a threading head for the shafts.
The largest threader I had was 14mm and it went without a problem, but the thread is not very deep despite using a 12mm thread drill.
.
You can see the entire stage from the machine build and testing in the video below.
I encourage questions and comments.
.
I wanted to introduce my next design which is a threading arm.
The base of the machine is a 400 kg magnetic lifter ordered from a well-known Chinese portal for the sum of 330 PLN.
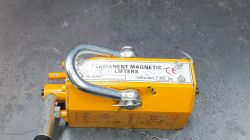
I bolted a flat bar to the top of the magnet with a welded 30 mm shaft. I then screwed linear bearings to the 80x80 profile on both sides and put the whole thing on the shaft.
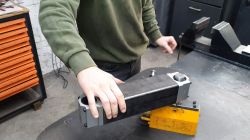
The next components of the arm are two 30x30 profiles which are supported by two 120 N actuators.
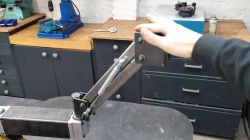
The last element of the arm is a screwdriver handle made of 15 mm sheet metal.
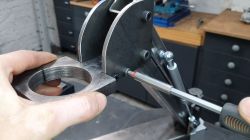
I also decided to make a threading head for the shafts.
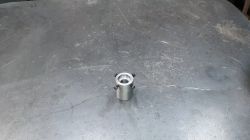
The largest threader I had was 14mm and it went without a problem, but the thread is not very deep despite using a 12mm thread drill.
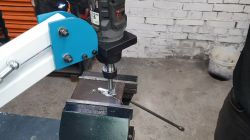
You can see the entire stage from the machine build and testing in the video below.
I encourage questions and comments.
Cool? Ranking DIY