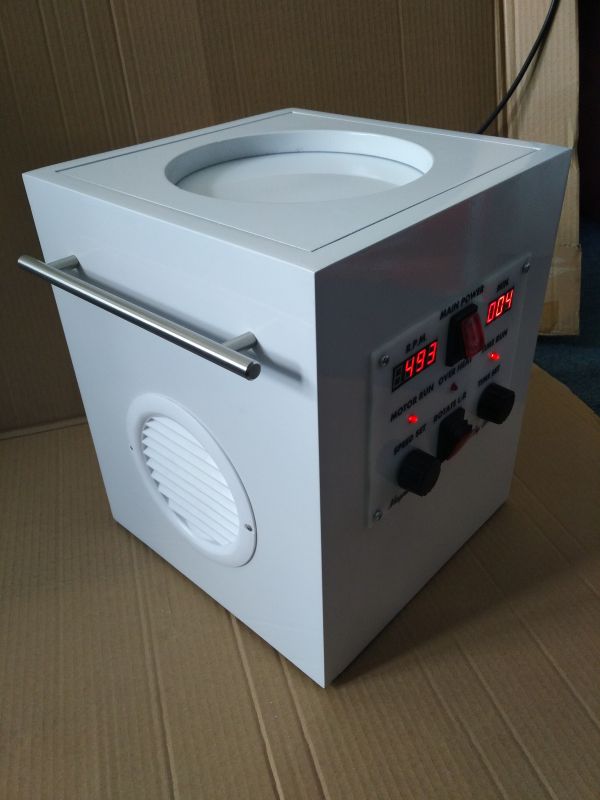
About three months ago a friend asked me if I would build a magnetic polisher for his friend jeweler. I asked what is it what is it? A longer discussion developed here, an exchange of a few e-mails / sms with links and I already more or less knew what a machine it was.
The general principle of operation is simple. We have a spinning "plate" on which four strong neodymium magnets are mounted. Two of them are placed close to the outer edge of the plate and directed upwards with the N pole, and the other two are close to the center of the plate and directed upwards with the S pole. This creates a kind of rotating magnetic field wave which alternately attracts and repels the material . And the material is needles ... But more on that later.
I will not write here about all the difficulties and problems encountered, because there was so much that the construction took 3 months instead of the planned 2-3 weeks.
I will briefly describe the resulting device and share photos. Maybe it will be useful to someone in the future. The cost of the part plus unexpected expenses is about PLN 1800 plus labor. In total, about half of what you have to pay for a similar factory polisher.
Now it's time for some construction photos, because that's what DIY is all about.
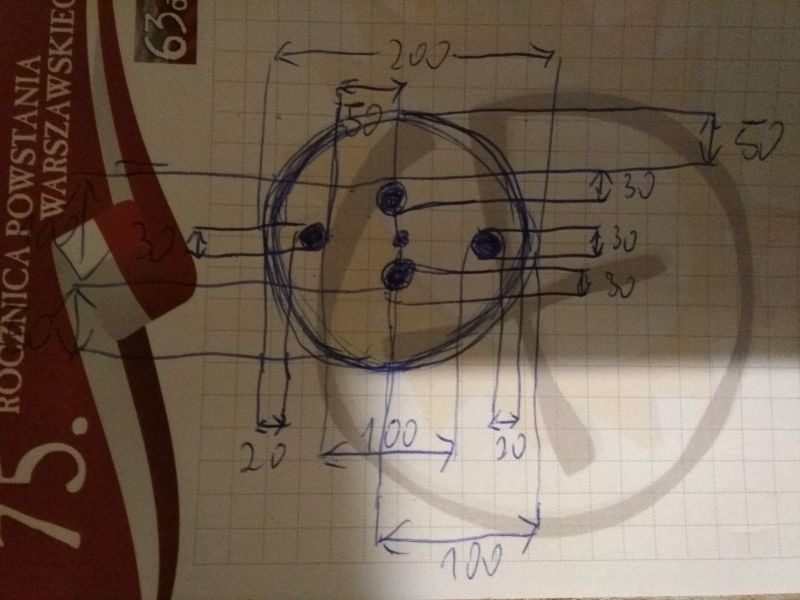
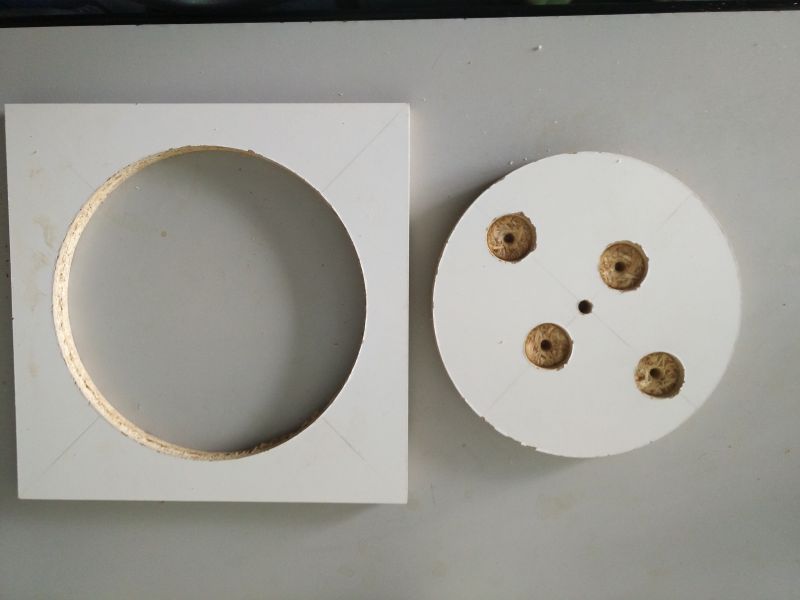
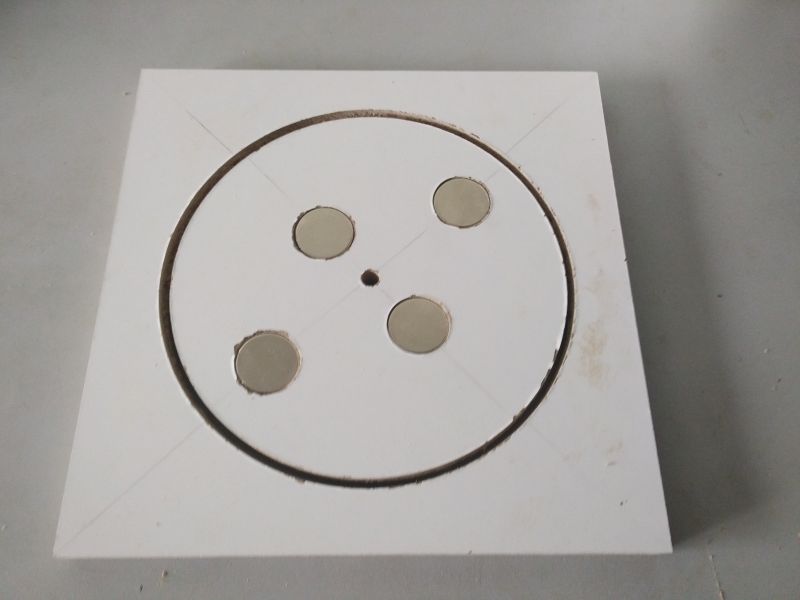
It was the plate.
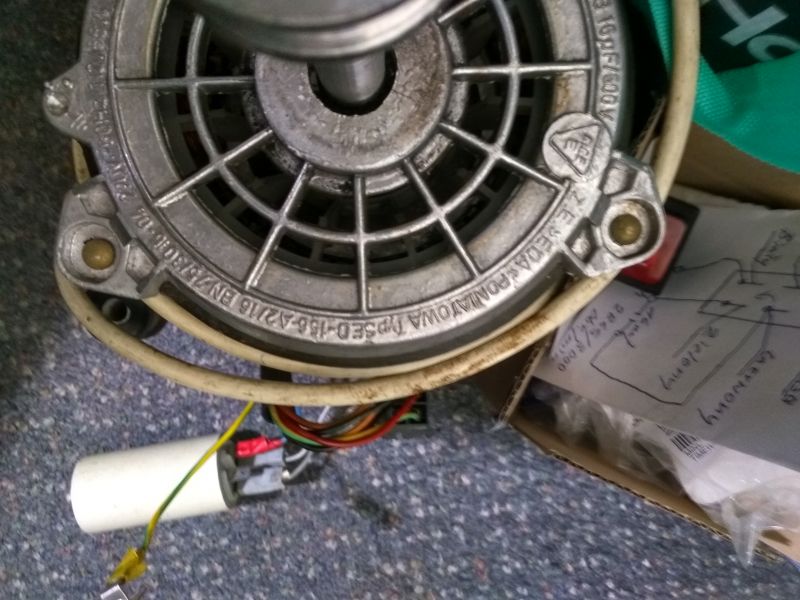
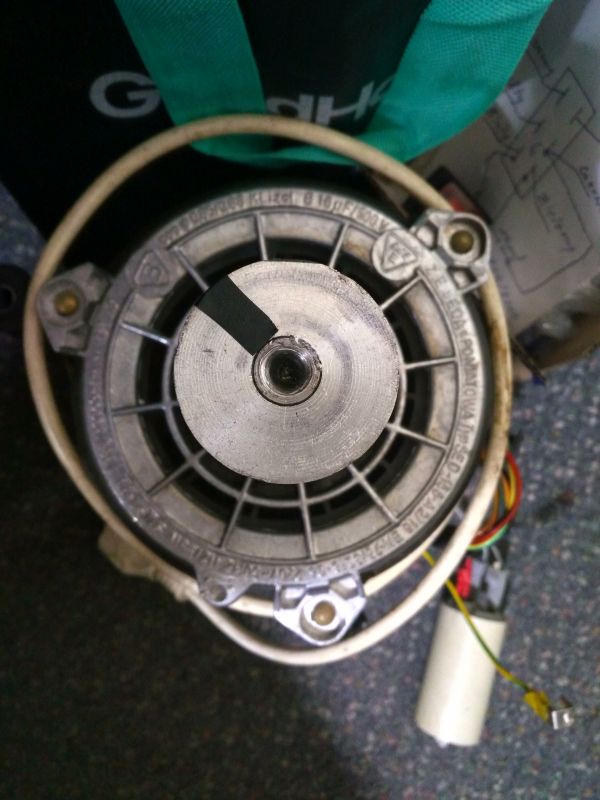
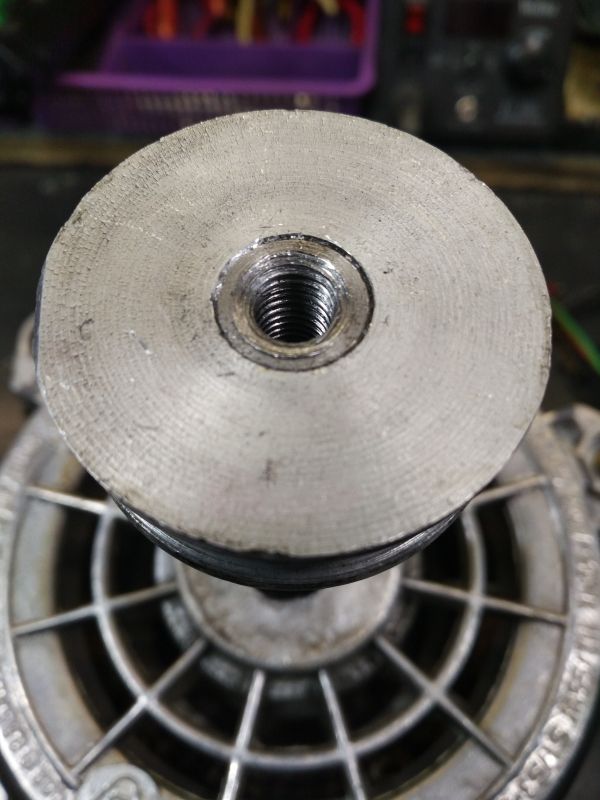
Here is the engine that turned out to be a total failure and had to be reworked to 3-F. For this I am proud of the thread in the shaft. As I couldn't pull off the pulley in any way, I drilled and threaded the motor shaft. Not having taps for blind threads.
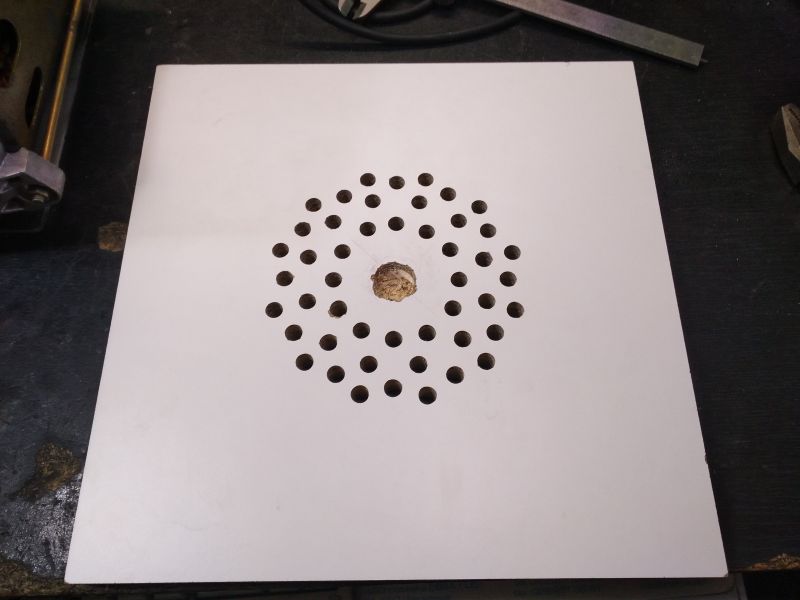
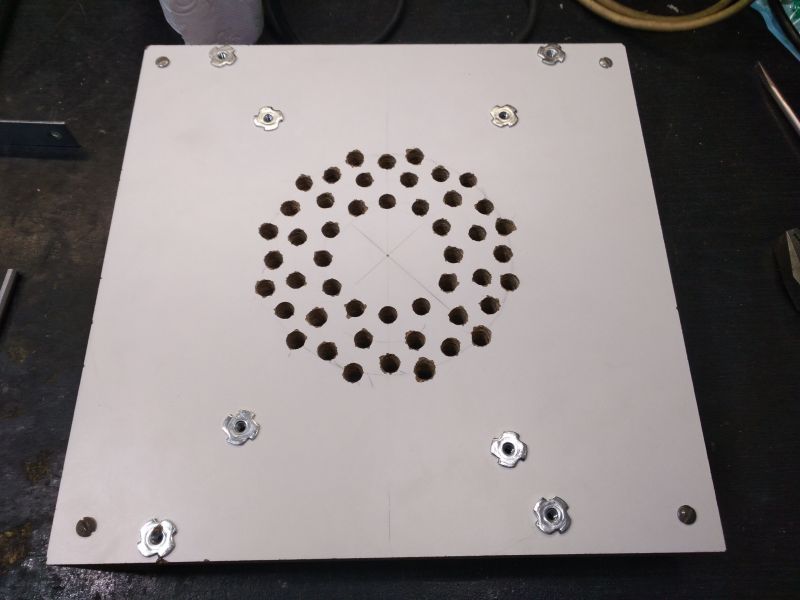
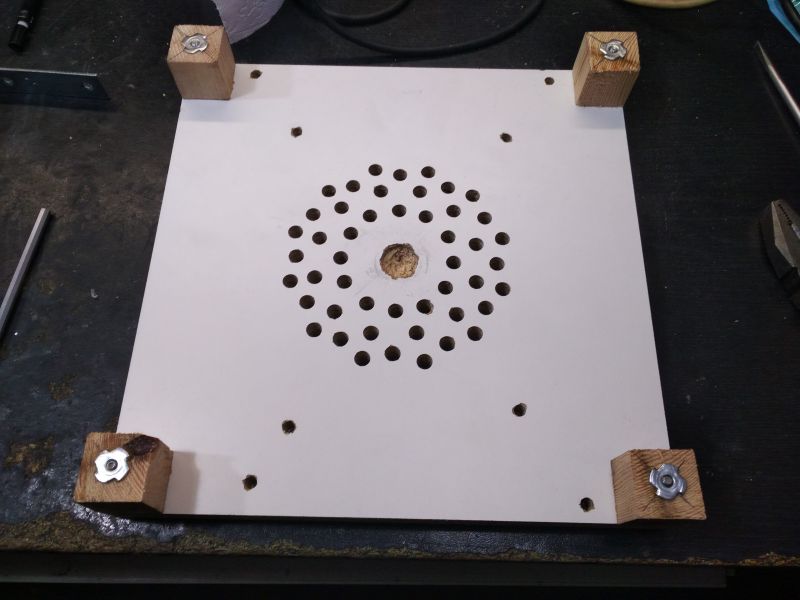
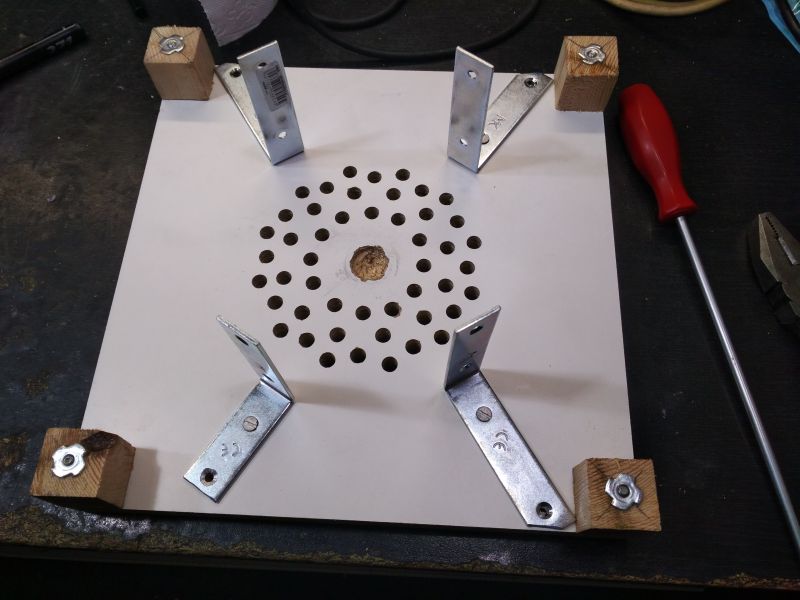
Bottom of the housing and engine mount.
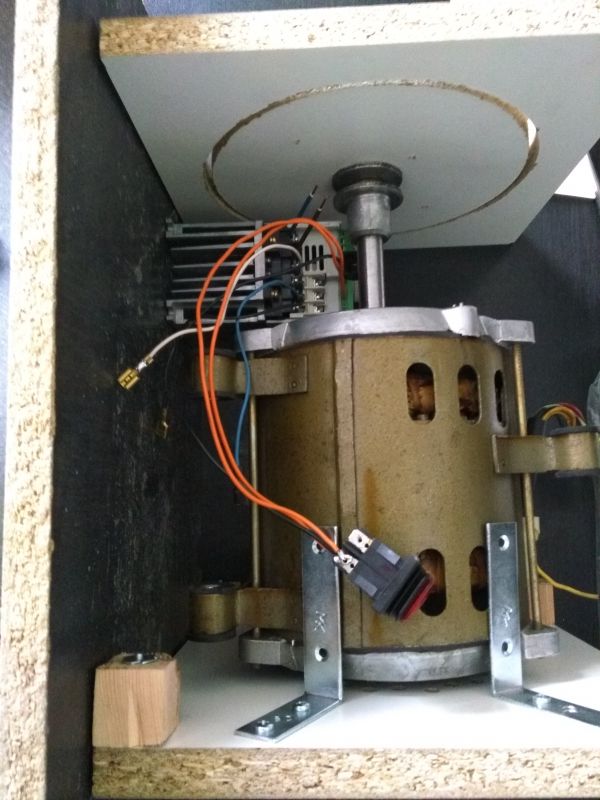
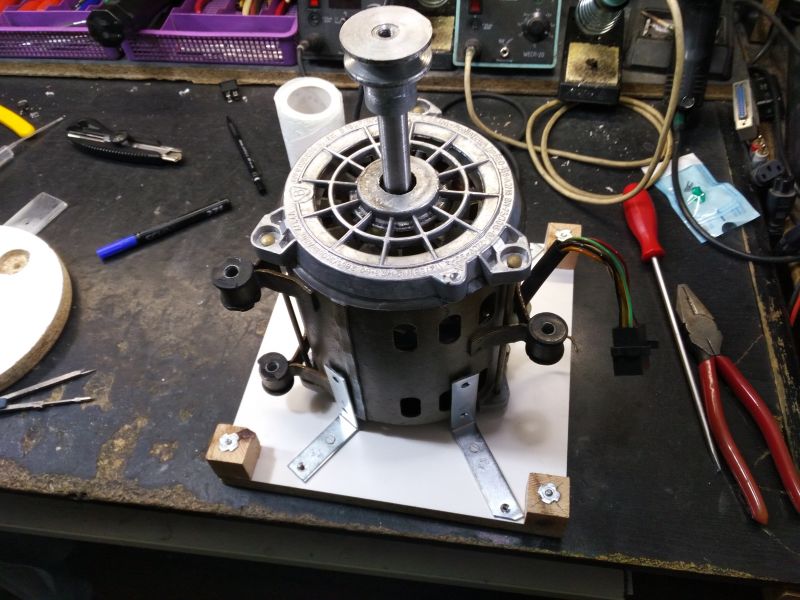
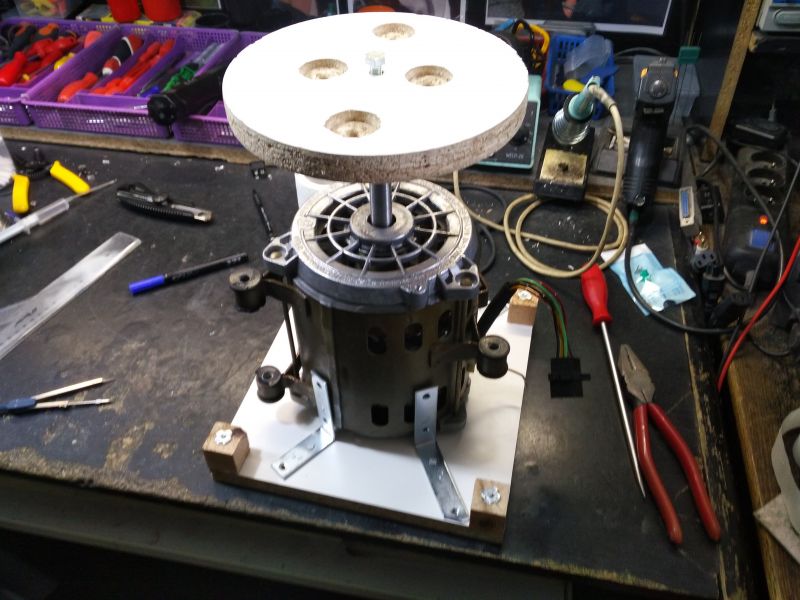
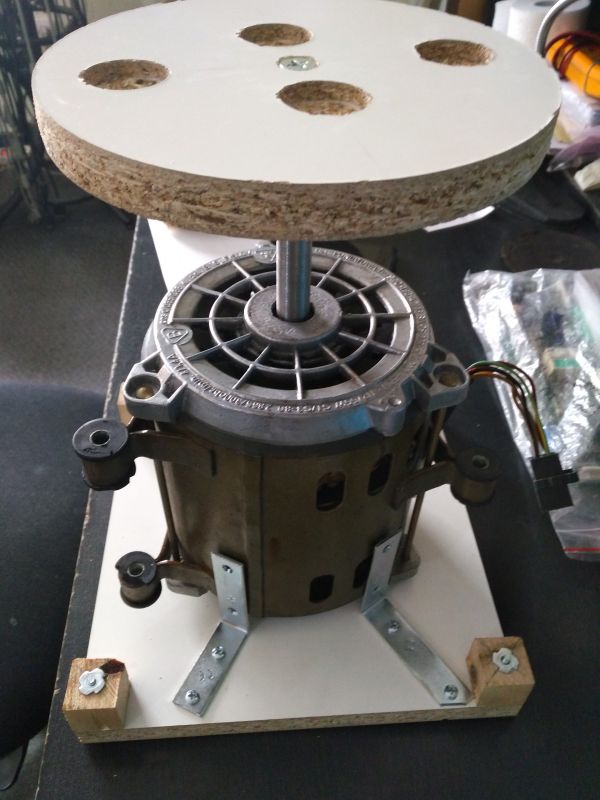
And here is the engine itself with a plate.
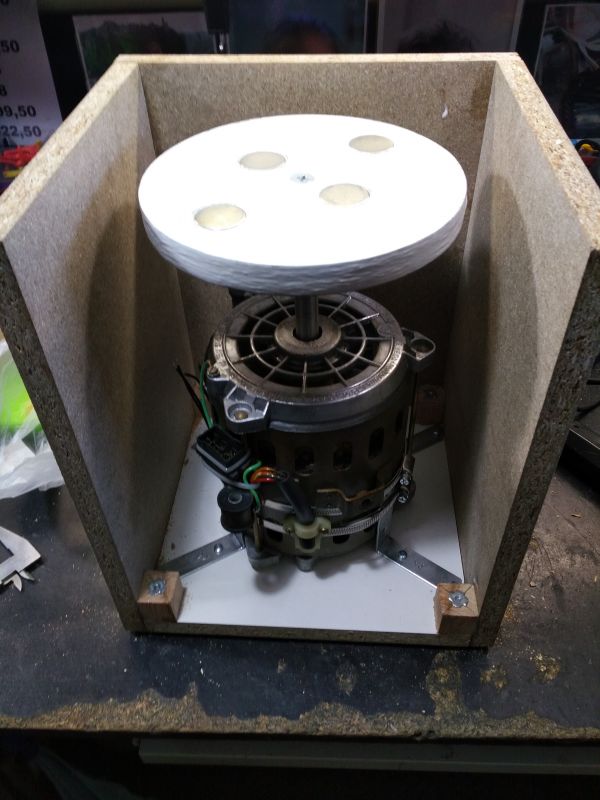
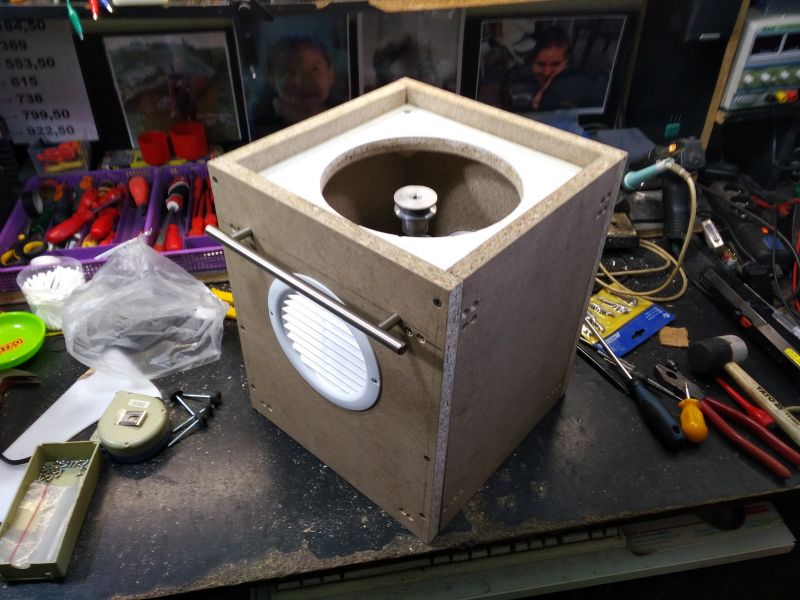
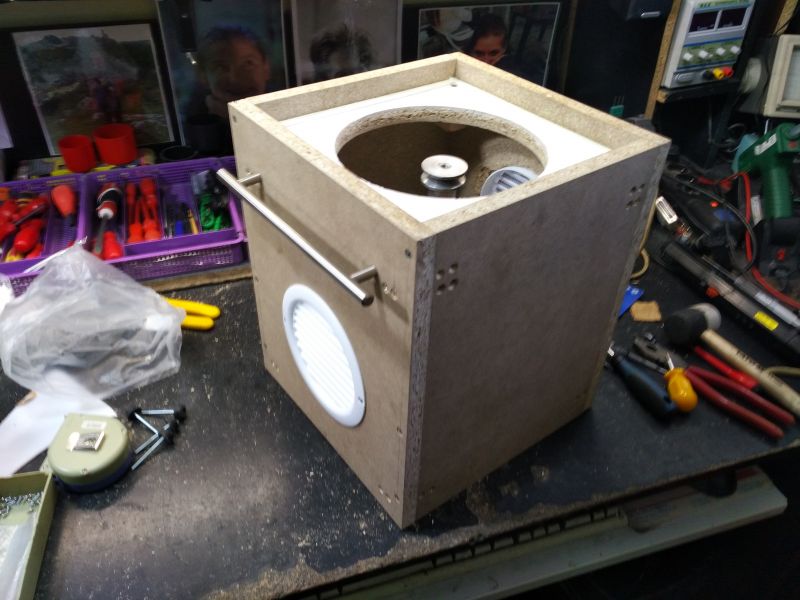
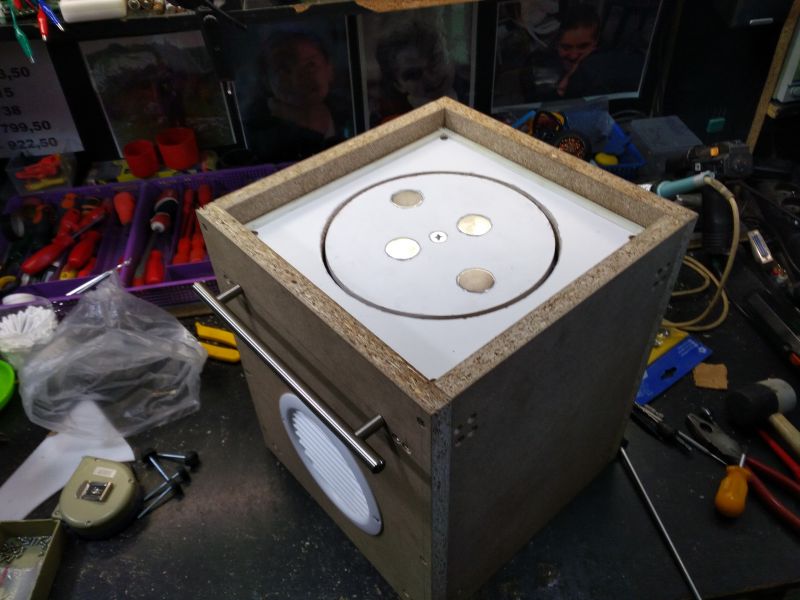
The work is moving forward, you can already see some outlines of the whole.
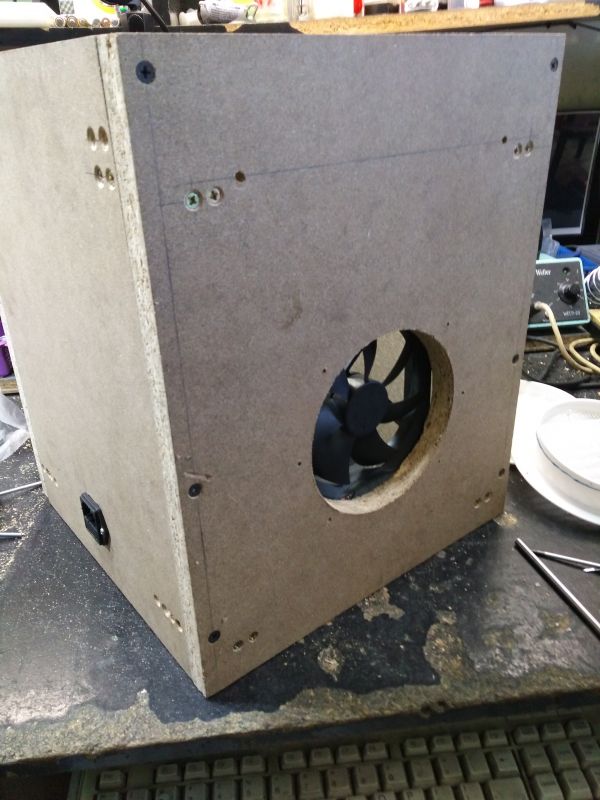
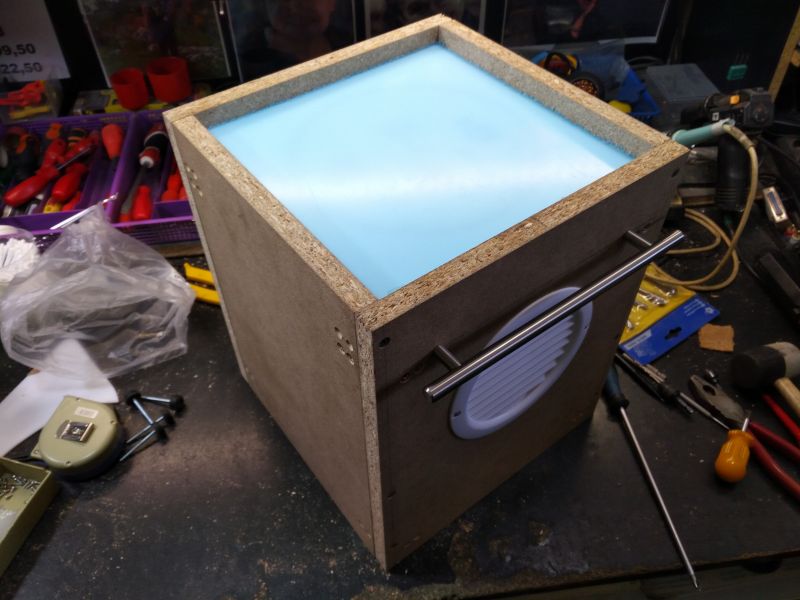
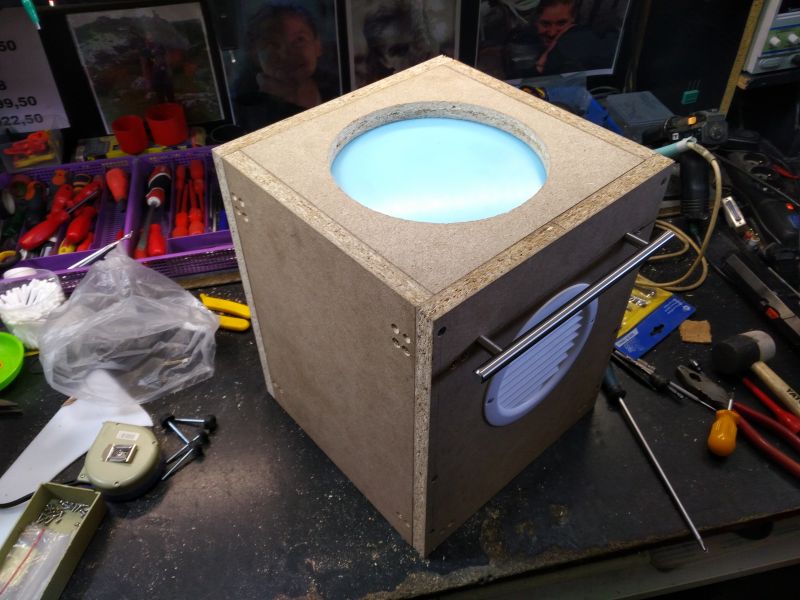
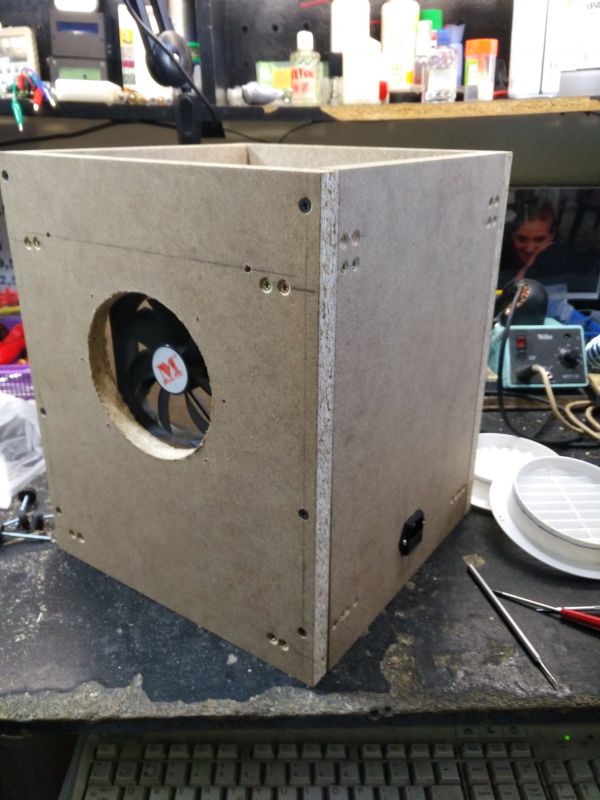
Closer to the final ...
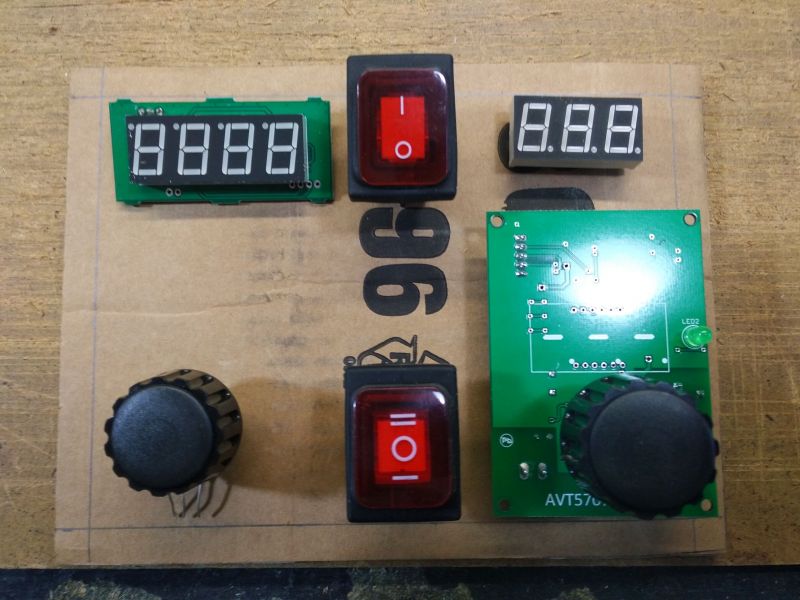
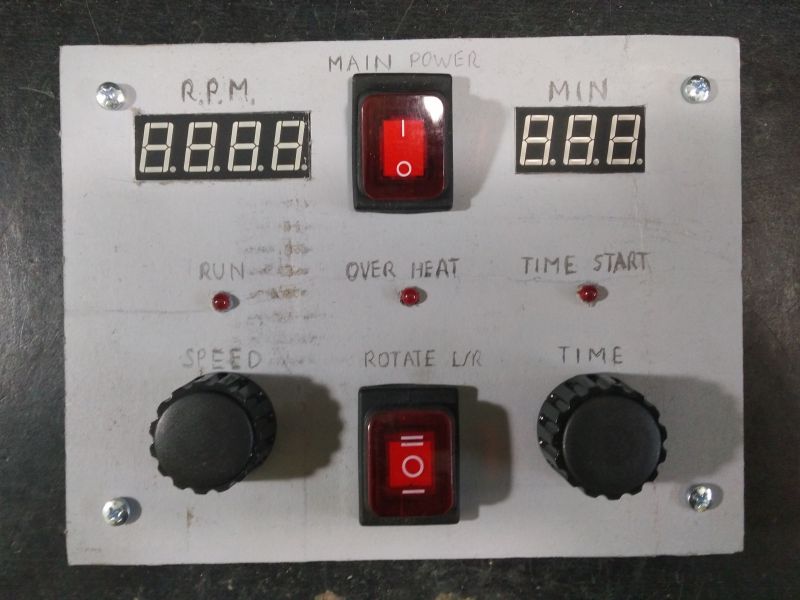
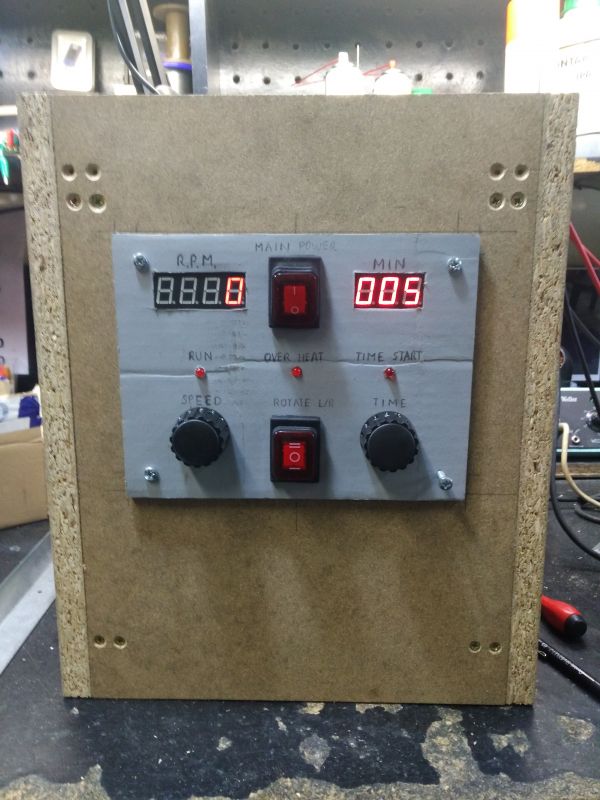
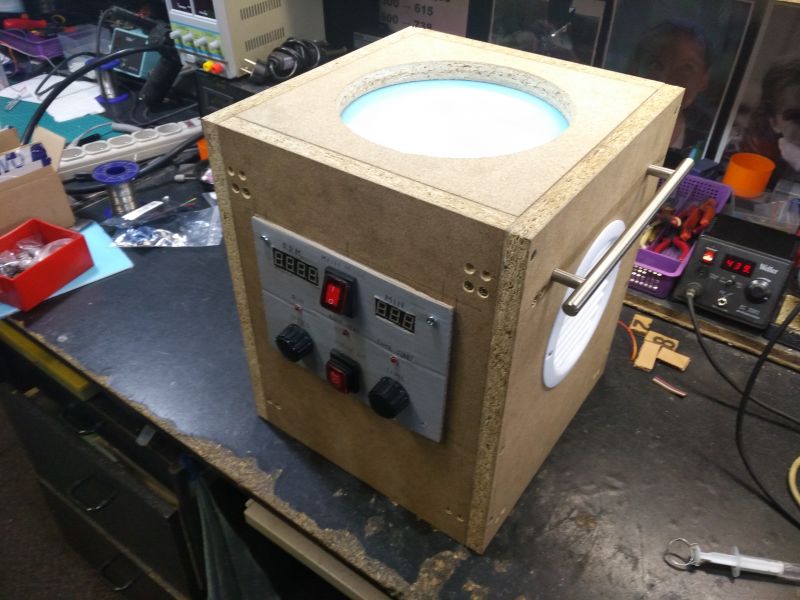
Preliminary design of the front panel made of corrugated cardboard with a scalpel.
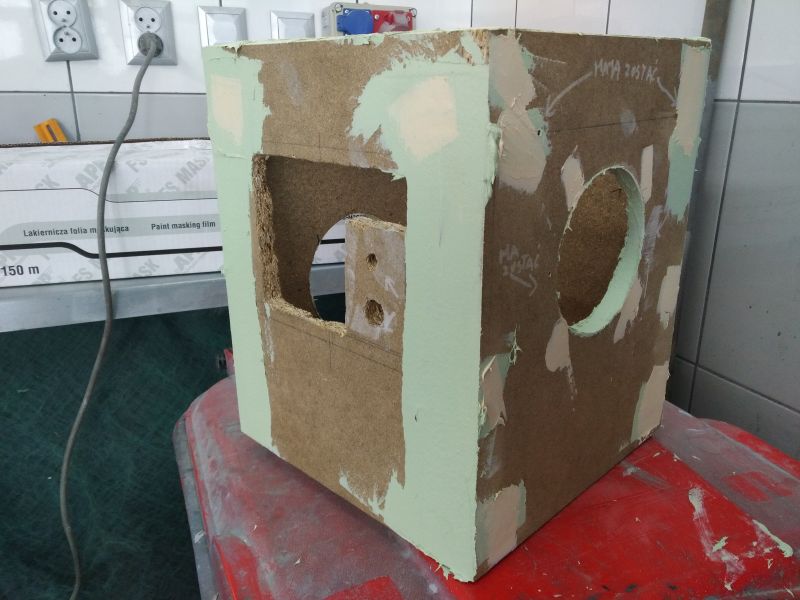
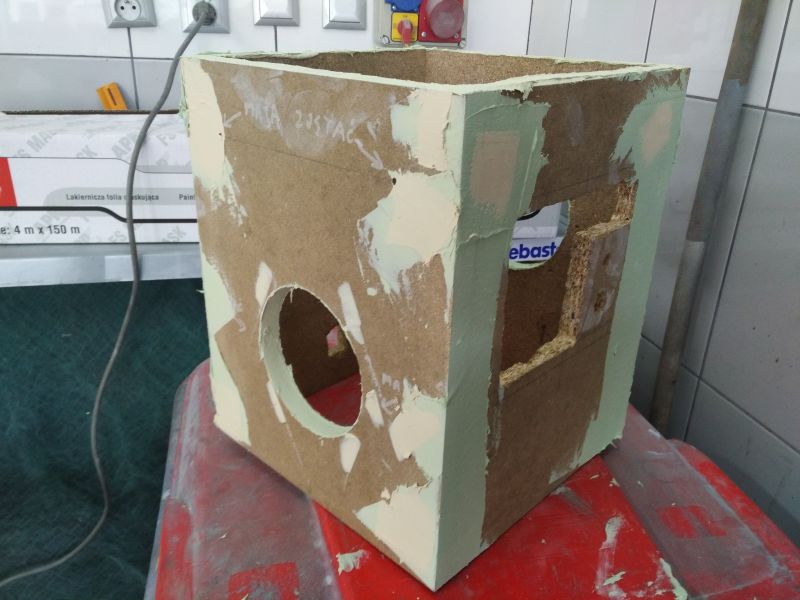
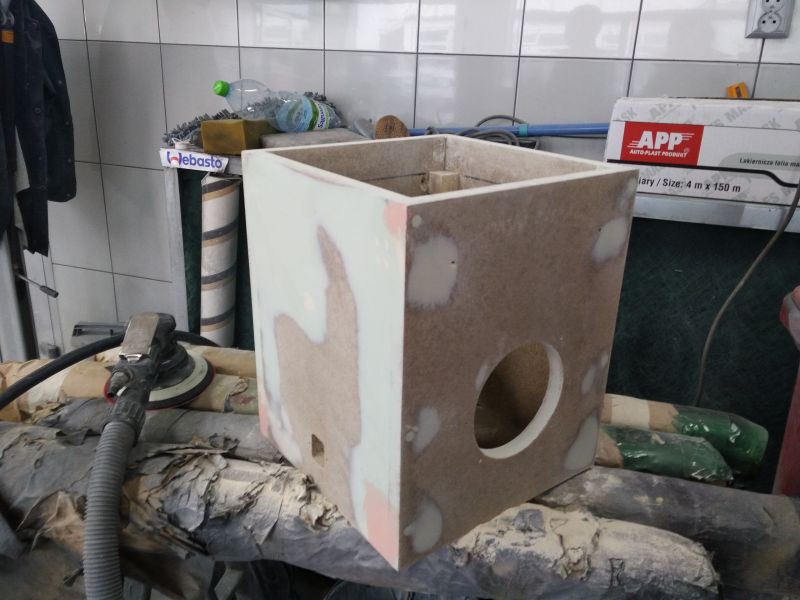
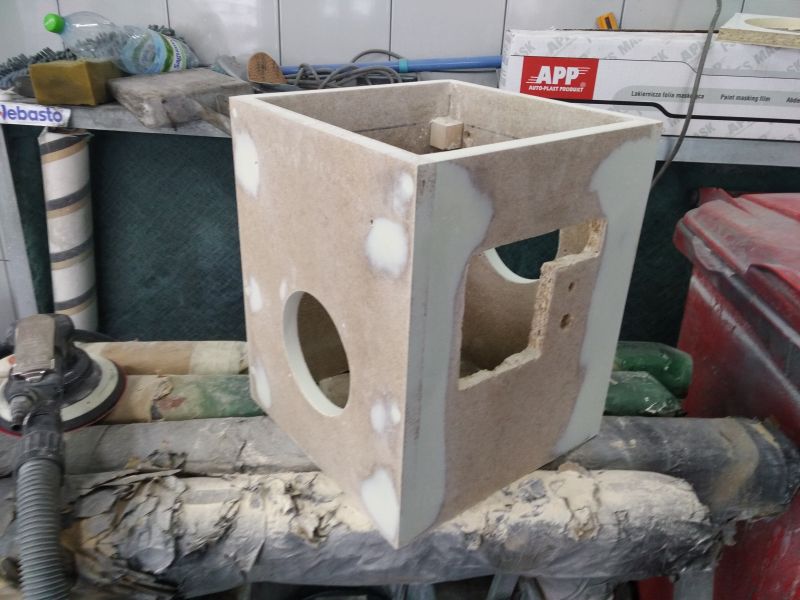
And here puttying ...
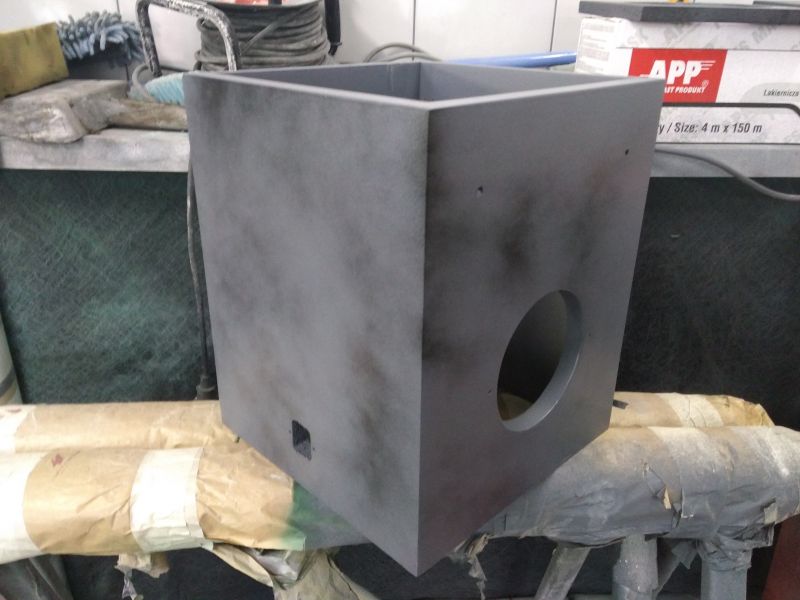
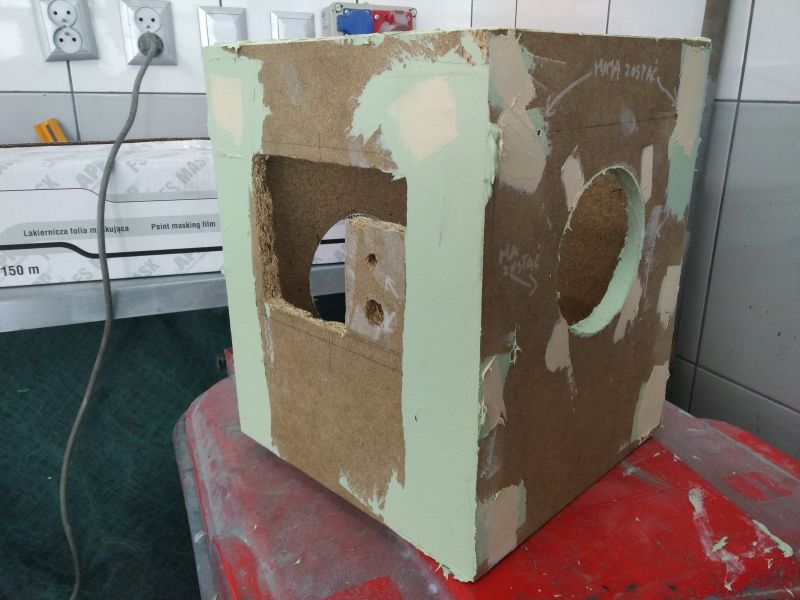
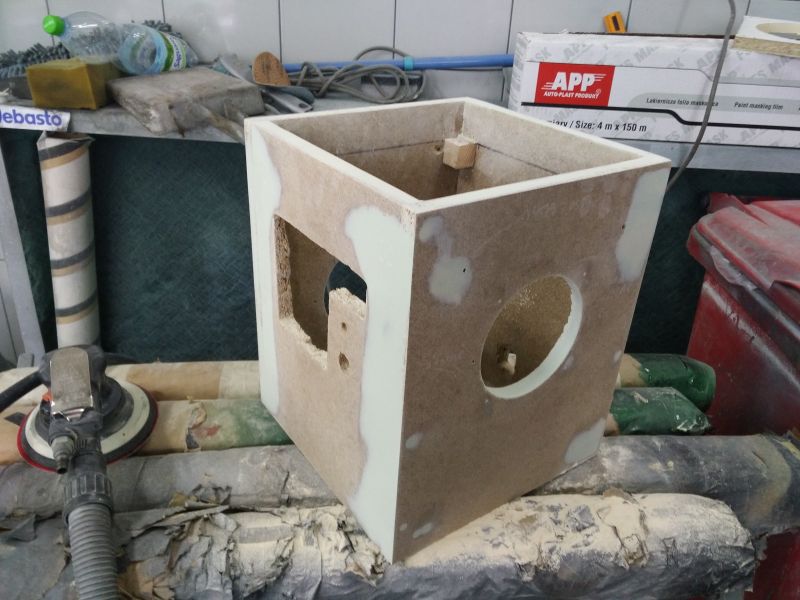
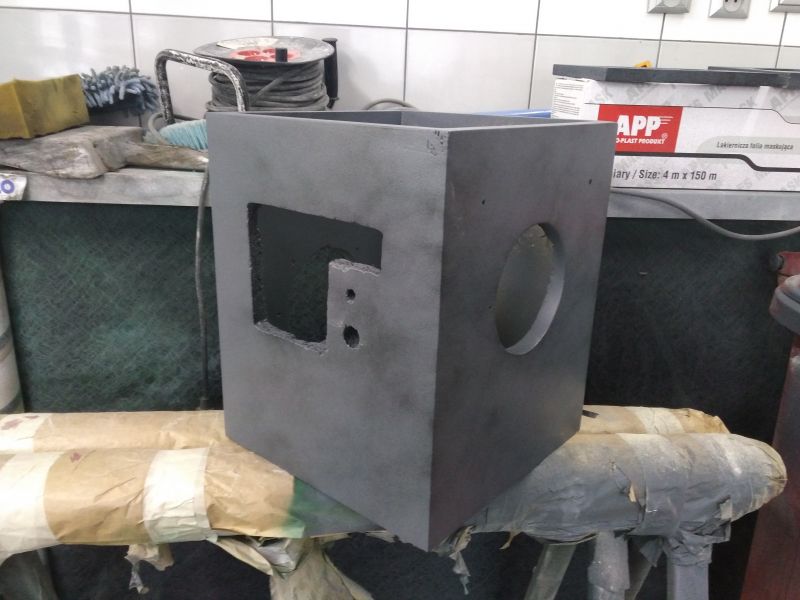
More putty and primer.
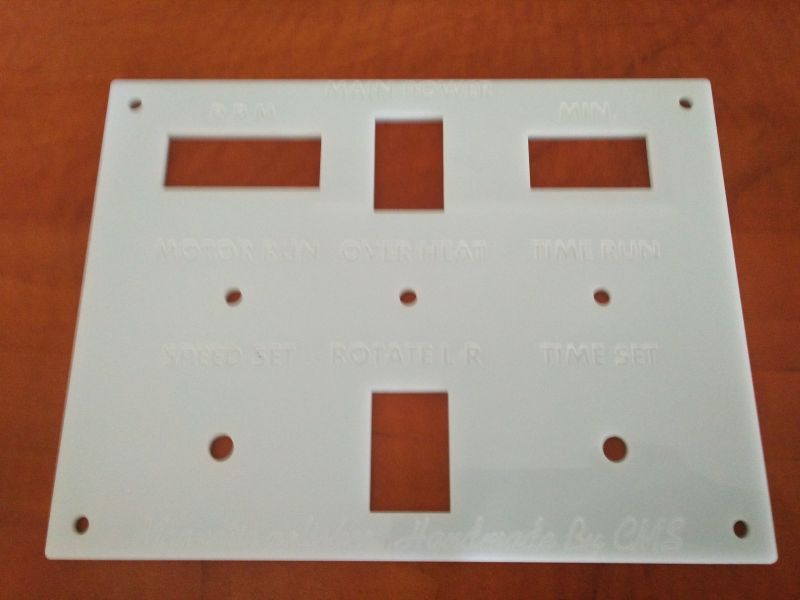
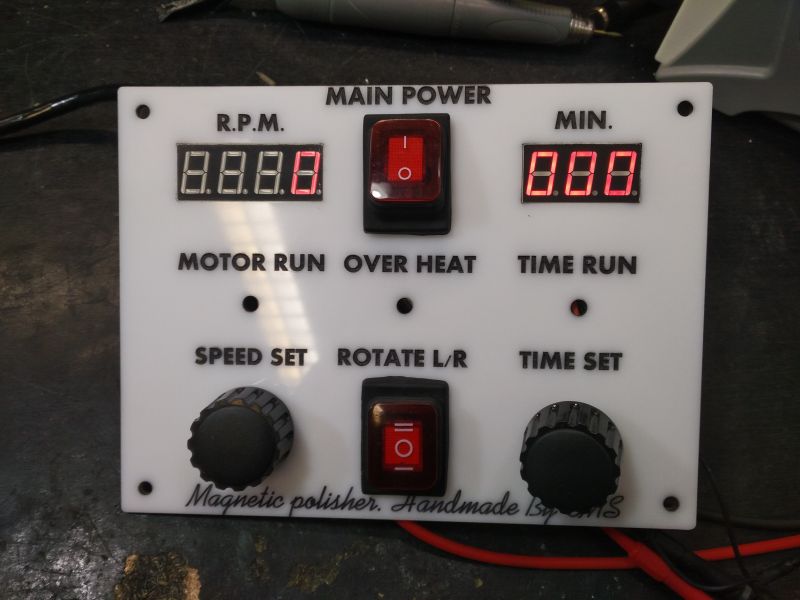
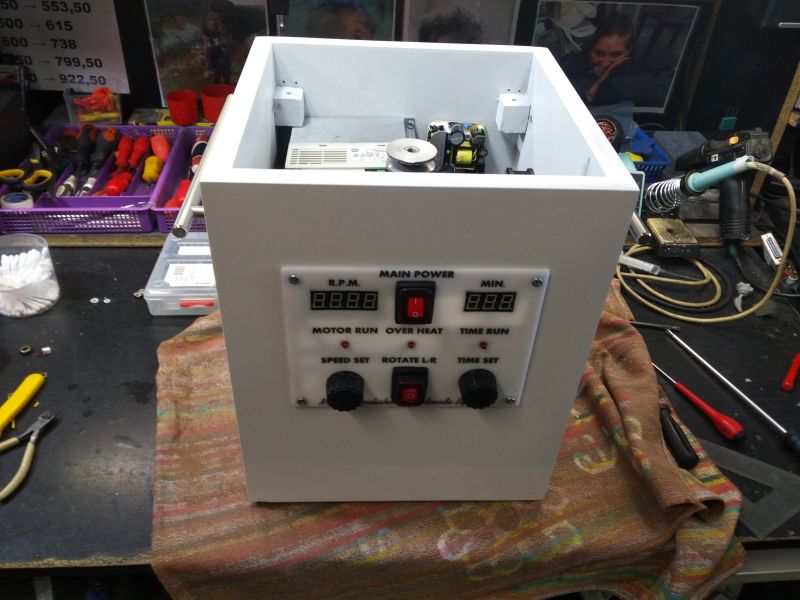
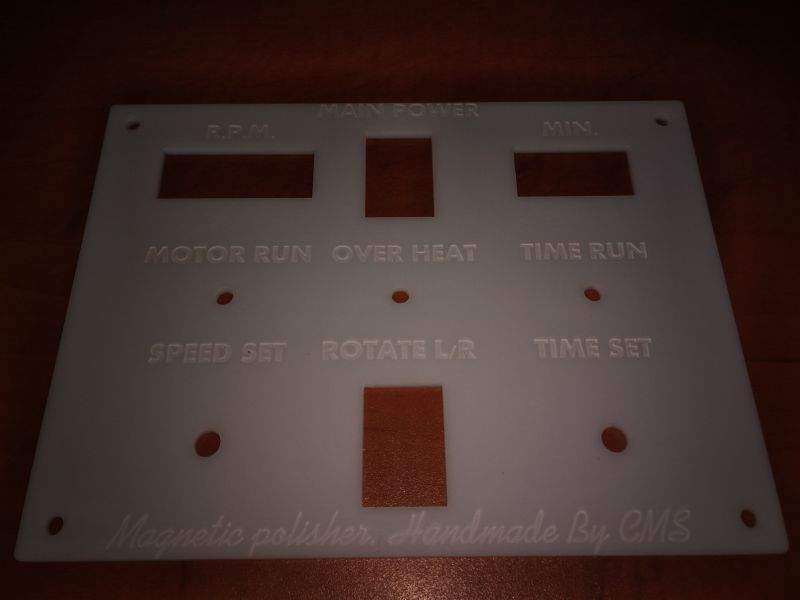
In the meantime, a front panel made of plexiglass was created, the inscriptions are engraved to a depth of 0.5 mm on a laser plotter and filled with nitro varnish.
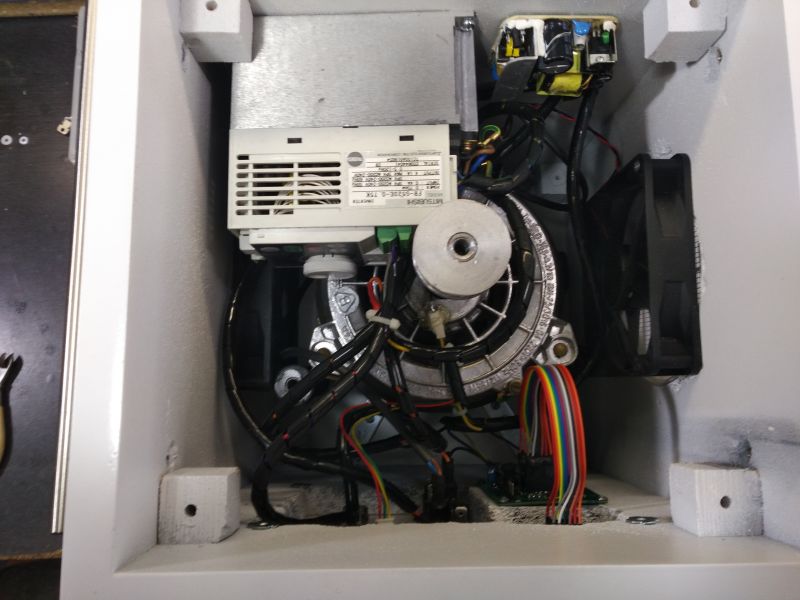
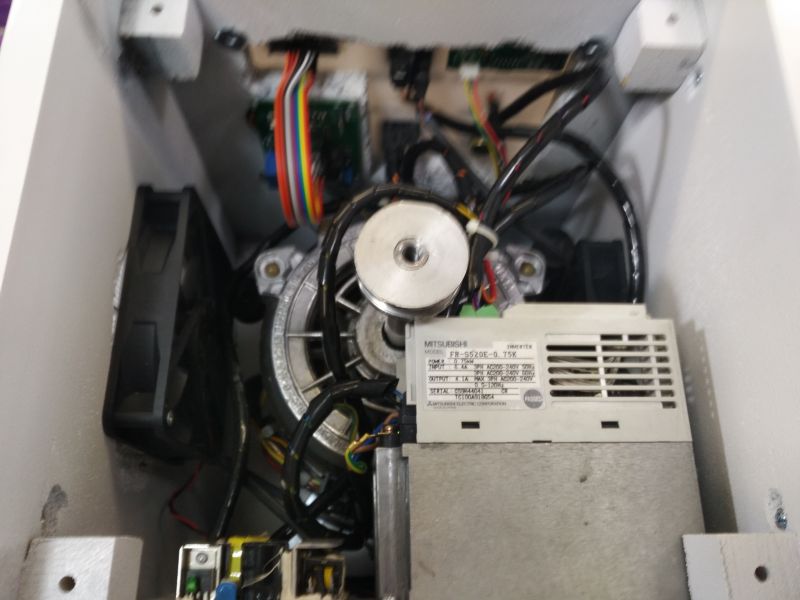
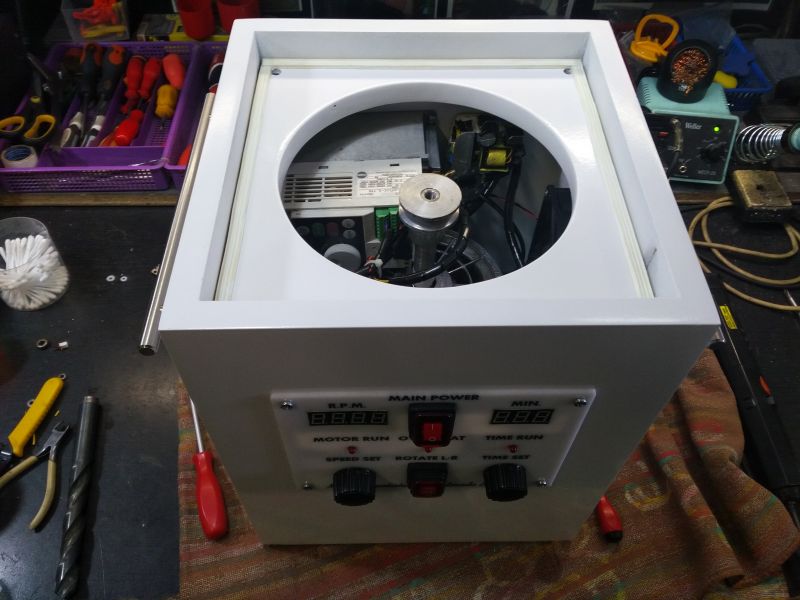
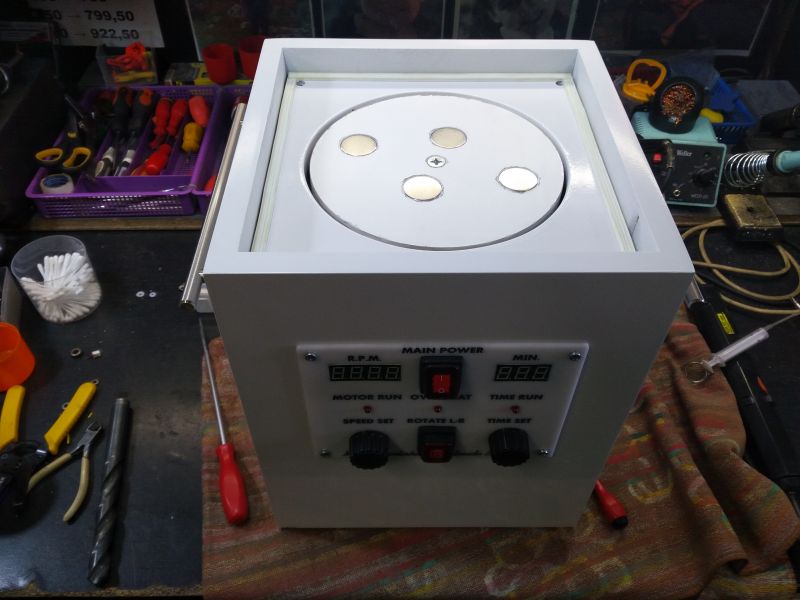
This is what it looks like inside.

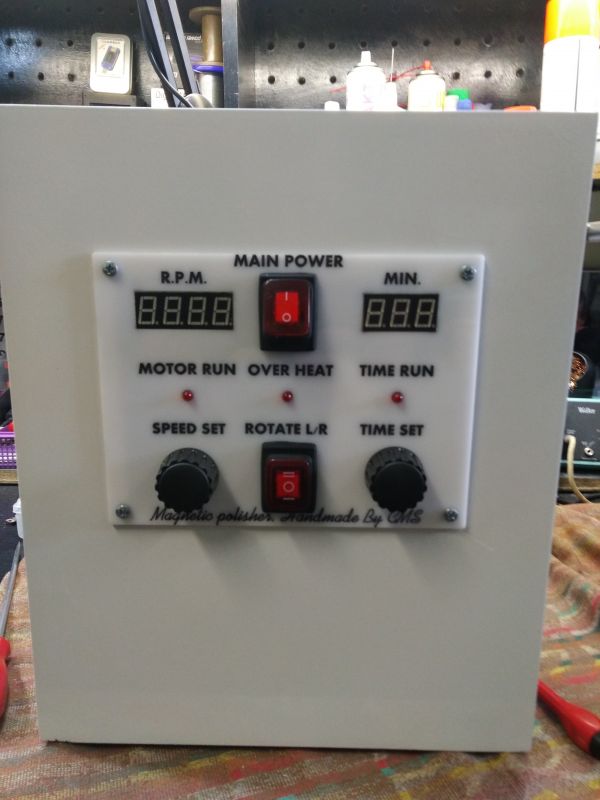
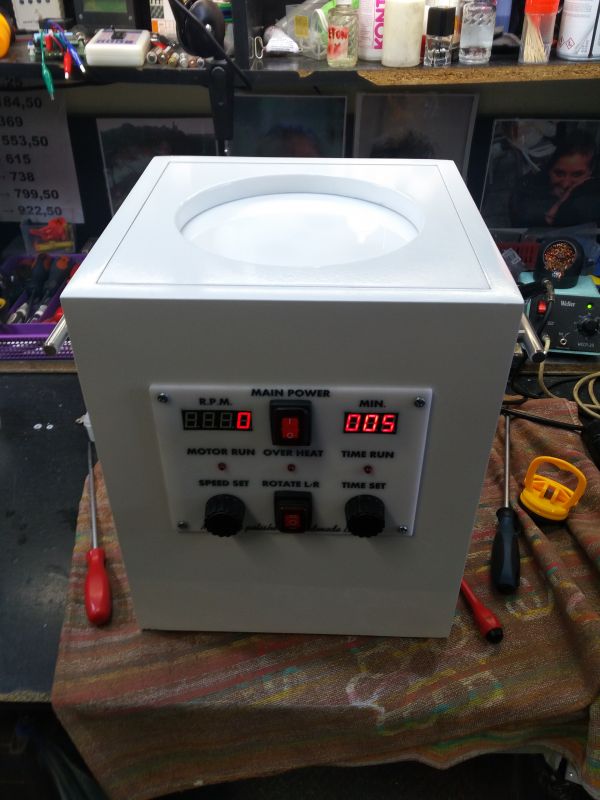
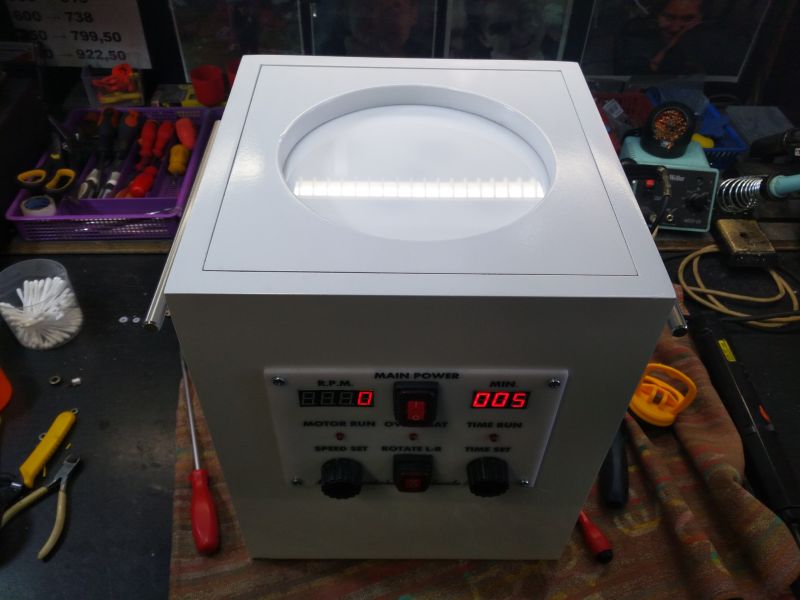
And so from the outside.
I am not going to post any diagrams or other documentation here, because they have not been created, and I will not create documents on purpose, since the machine is already at the customer's.
If someone is kumaty and needs such a machine, he will build it. After all, three months ago I didn't even know what it was ...
I just want to share some photos of the construction. Usually, I don't present my designs, even those of a high standard, because I don't have time for it. But this is the first time I have seen a device / machine of this type and this is the only reason why I am willing to share this construction with you. Because it's interesting.
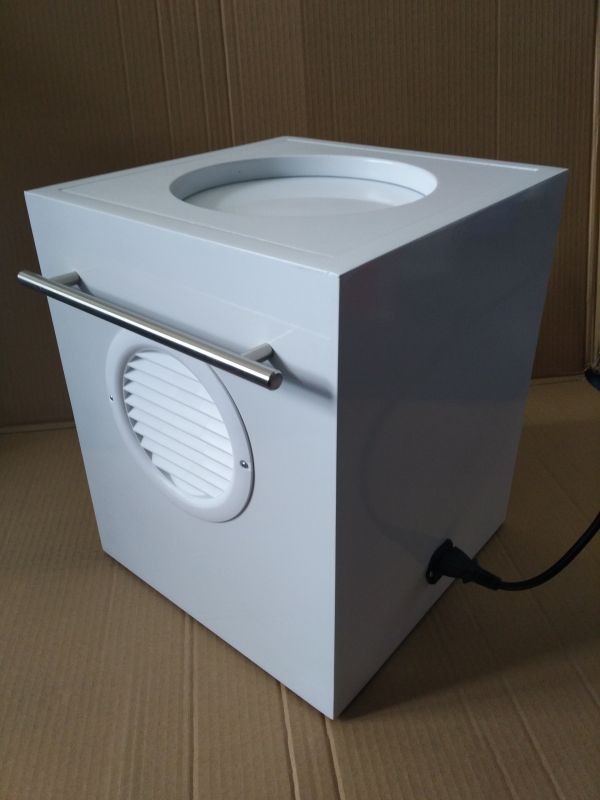
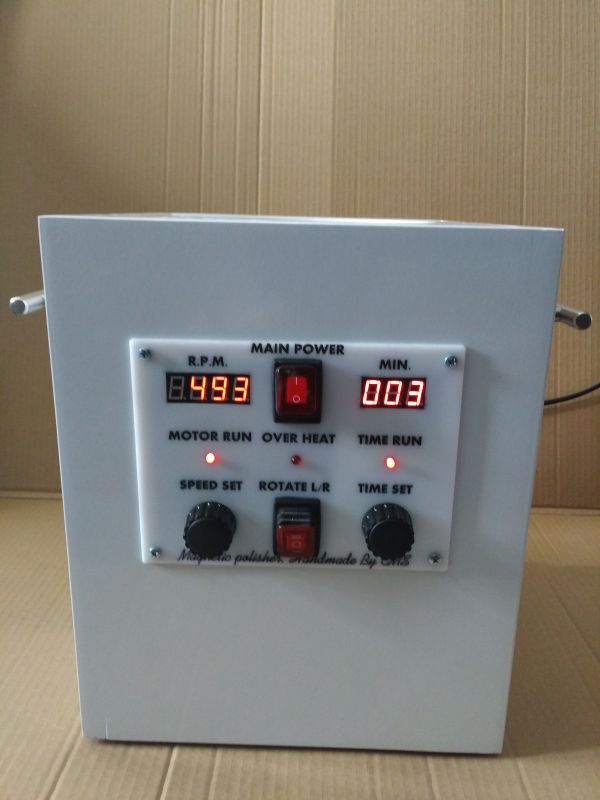
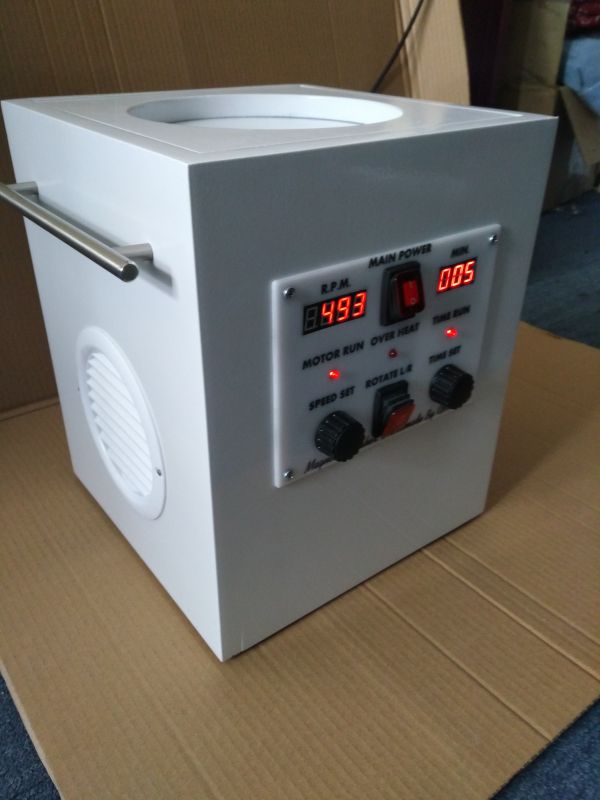
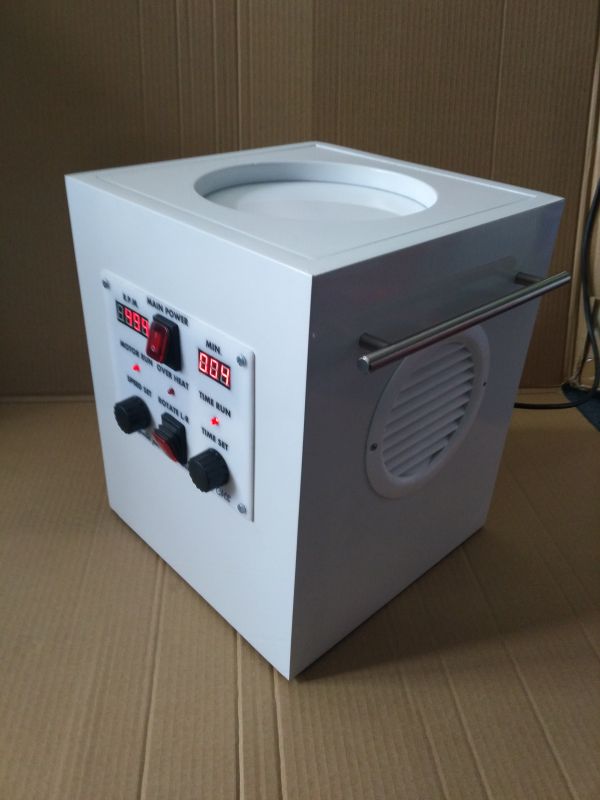
The final result.
As I mentioned, I will not describe the vicissitudes of the entire construction, because it would take as long as the construction itself. You have pictures to see and read, a few sentences of text.
Maybe I will mention the security features.
If the motor housing exceeds 50 ° C (which did not happen during the tests), the fans will start.
If for some reason (despite the fans running) the motor reaches 85 °, the power to the inverter will be disconnected (the fans will, of course, remain powered).
And there is also an ordinary 20mm glass fuse.
At this point, I would like to thank my colleague BESTLER for this
any technical assistance and encouragement in the moments when I already doubted this project.
Cool? Ranking DIY