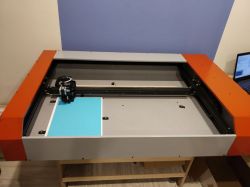
Today I present a CNC machine - a plotter with a drag knife which I made for my own use (for my spouse).
The spouse designs and cuts out decorations from paper. So far, he uses the Brother Scanncut plotter. The machine works quite well, although after cutting, I think that already thousands of decorations show some wear. In addition, it works quite loudly, which is a bit disturbing because the studio is at home (the engines probably work at full speed, the housing vibrates a lot) is slow and the working area sufficient for an A3 sheet has started to be insufficient.
A decision was made to build a new machine with a larger working area.
Initially, the idea was for a laser. Despite my concerns about inserting the laser into the house (need for extraction, flammable material, etc.), I took the first steps. I bought a 30W laser and to speed up my work a bit, I also bought a 165 x 85 cm frame according to the openbuilds project. In the meantime, however, it was decided that a drag knife would be the best solution for this application. The already purchased frame, a bit too flexible for a drag knife, but for the one without the Z axis, I decided to use it. I made the Z axis myself, a trolley with a head holder printed on a 3D printer. I strengthened the frame and mounted it in the reverse position. Initially, I wanted the axle to be light and I wanted to use a modeling servo as a drive (see the photo), but I quickly found out that it was a bad idea. Finally, the Z axis drives the stepper motor, the pressure of the knife by a push back spring.
The housing is mainly plywood and MDF (used scraps and waste that I had) and 0.5mm steel sheets as covers. There is also a table with shelves for mats and paper.
The paper mats are 6mm foamed PVC with scales engraved on the milling machine to make it easy to arrange the paper.
Controls are GRBL and CNC Shield, on Universal gcode sender computer.
Since it was hard for me to find a tool that would be simple, easy and quick to generate the toolpath, I did my job. This is the program I called CuterCam and it was this stage that took the longest (about 1.5 months).
The program loads a dxf or svg drawing, detects the shapes itself, determines the order based on the algorithm. Shapes can be moved, rotated, duplicated, deleted, hidden, grouped etc. and arranged freely on the selected mat. In fact, it takes just a few clicks and the g-code is ready for a very complicated drawing. The program has a wizard of post-processors, you can create and save many of them. Shapes are cut out according to one of 3 algorithms:
- internal first
-external first
-nearest shape
In addition, the program allows you to control the angle of the knife entry. After completing the previous shape, the program saves the knife setting angle (angle of the last vector of motion) and starts the next shape from the place where the angle of the first vector of motion is as close to it as possible. This allows the knife to be lowered immediately to the cutting direction, it does not have to turn back in place, so there is no risk of breaking it or tearing the material out when turning.
Below are some photos that have survived from the construction and a video of cutting out and the work of the CuterCam program.
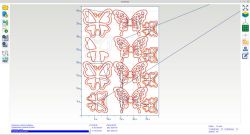
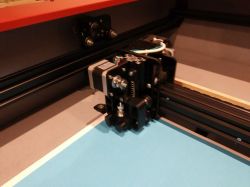
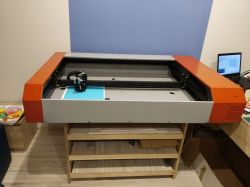
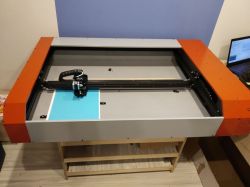
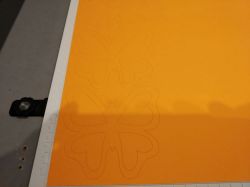
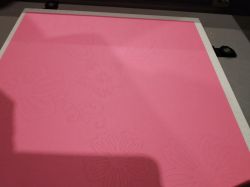
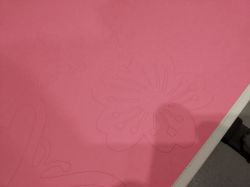
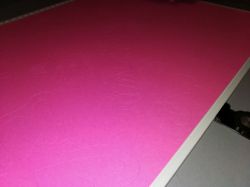
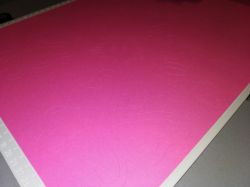
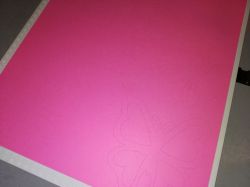
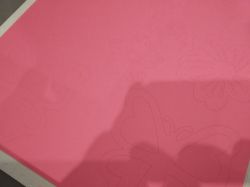
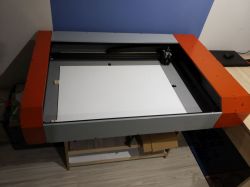
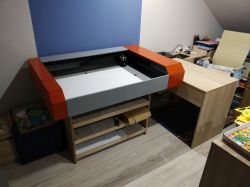
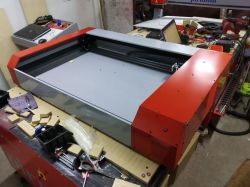
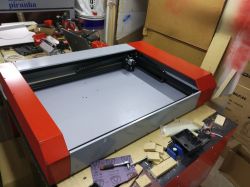
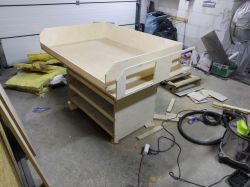
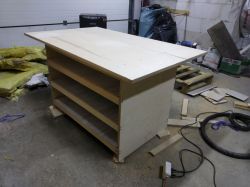
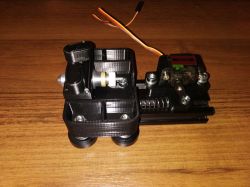
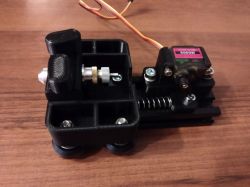
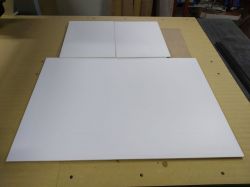
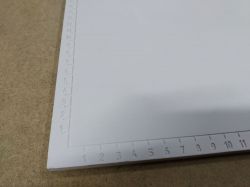

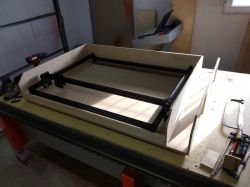
Cool? Ranking DIY