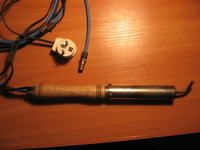
Hello. I made a soldering iron for plastic. I saw a similar company, and that the construction is very simple and you have to pay for welding, it is worth doing. 5mm diameter, 2m of hose, a piece of cable with a plug. The required pressure is 0.5 ÷ 1.5 bar. I used a simple regulator on a triac to regulate the heater. And the cube to connect the wires with the spiral is made of ceramic. Of course, not all plastics can be welded. As electrodes, I use the same plastic that I should weld. I cut strips with a width of 2 ÷ 4mm. After a few attempts, the welding turns out very well. I saw the company one for PLN 140, that's why I did.
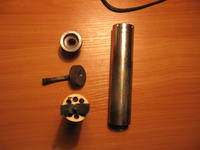
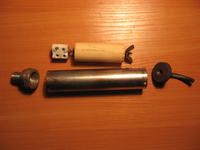
Cool? Ranking DIY