mastad wrote: Mr. Krzysztof. In the New Year 2019, I wish you all the best and wish you all the forum members.
I read this substantive thread carefully and I have a question. I have a 12V / 250VA troid transformer.
1. Can I use it for this project and what will the output parameters be?
2. If so, what modifications would I have to make?
I would like to add that it usually does not operate with voltages greater than 18V and 5A currents - usually 6, 9 or 12V. Builds guitar effects and sometimes digital controls for them. Thank you in advance for your answer.
Hello
Forgive me for answering so late, but better late than never.
Probably, my friend, you have already dealt with another power supply project and that would be understandable.
However, I will try to answer your questions, because it may be useful to others who would also like to assemble this power supply with a similar transformer.
You have a 12V / 250VA toroidal transformer, i.e. the secondary winding can be loaded with a current of about 20.8A.
In order for this power supply to fully show its efficiency and effectiveness, a transformer with a secondary winding with a voltage of 27..28VAC / 12 ... 15A must be installed. .
From this it follows that the voltage of 12VAC on the secondary of your transformer is not enough for this power supply, why I will explain this below.
Sometimes the secondary winding in more powerful toroidal transformers is wound simultaneously with two identical conductors.
If the secondary winding in your transformer is similarly wound, then after disconnecting the ends of the windings and connecting them appropriately (see the attached drawing), it can be used in the power supply discussed here.
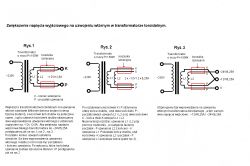
After connecting the windings as shown in the figure, your transformer will have a voltage on the secondary of 24VAC with a current load of up to 10A.
And with a transformer converted in this way, you can build this power supply with an output voltage adjustable from 0 to + 20V.
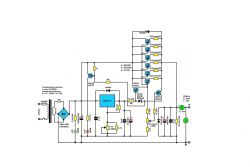
Looking at the diagram, it is not difficult to notice that the secondary winding does not have the so-called tapping.
Such a tap on the secondary winding with a lower voltage would certainly help to reduce the loss power of the control transistors when lower voltages are set at the output of the power supply.
But...
It turned out that in this power supply, at low input voltages, e.g. + 21V (this voltage is obtained from the rectifier, when the transformer's secondary winding is e.g. 15VAC / 10A), the current efficiency at the output of the power supply drops to 4-6A in the regulated voltage range 0 ... + 12V (15V). And just such a low current efficiency of the power supply (6A) was indicated by colleagues in previous posts, when they used transformers with a secondary winding with a voltage of 15VAC / 10 ... 20A or attached a direct voltage + 20V to the input of the power supply.
And yet the power supply should work efficiently with a load current of up to 10A ...
On the other hand, when the voltage at the input of the power supply was greater than +38 ... 39.5V (this voltage is obtained from the rectifier, when the secondary winding of the transformer is 27 ... 28VAC / 10A), the current efficiency of the output regulated voltage is 0... + 25V was kept almost in the whole range at the level of 8-10A. Due to the lack of this tap, I used 6 control transistors to maintain the maximum current efficiency of the power supply with large power losses.
With such a number of control transistors, the large power losses will be divided into individual transistors, ensuring their safe operation when the power supply output is loaded with the maximum current at low voltages set at the output of the power supply.
For the safe operation of the transistors, a heat sink with appropriate dimensions should be used, along with additional cooling through forced air circulation by means of a fan (s).
If, however, it is not possible to increase the voltage on the secondary winding in your transformer (250VA - 12VAC) due to the fact that this winding is made with one wire, I suggest connecting an additional winding to the factory secondary winding in the amount of about 42 coils.
Wind the wire in the same direction as the factory winding and the same diameter as the factory winding, then connect the start of the additional winding to the end of the factory winding and we get a voltage of about 24VAC / 10.4A.
By increasing the number of turns to about 52, we get a voltage of about 27VAC / 9.2A on the secondary winding.
If the transformer conversion could not be performed, it remains to use a voltage doubling rectifier.
It's not a perfect way, but it does the job.
Once, for the test, I assembled a rectifier in such a connection system with a 150VA - 12VAC / 12.5A transformer and with a load of 5A at the rectifier output I got + 19V ...
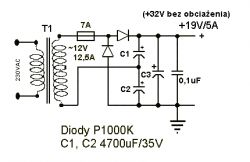
You wrote my friend like this:
"I'll add that it doesn't usually operate with voltages greater than 18V and 5A currents - usually 6, 9 or 12V. It builds guitar effects and sometimes digital controls for them."
Therefore, using a voltage doubler rectifier you will be able to build a power supply as below with an output voltage of 0 ... + 15V with a current efficiency of up to 5A.
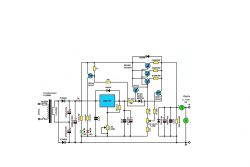
greetings