I tried very hard ... renovation, finishing, tiredness ... hit me too.
The cable is cut solidly, in such a stupid place that I am ashamed to admit that I marked the place for a new box myself. Let's do it for fatigue and that's the end of the topic.
I decided to document the repair process so as to take advantage of this fact and officially write on the electrode how, in my humble opinion, you can properly connect the cables in the wall, if you want to avoid the box. The subject is called "roast me" because I know what writing about THESE things on the electrode can be.
Luck - the condition is such that I can easily remove and replace the cable part for the top box.
I decided to deal with the matter systematically and neatly.
For various reasons, I did not want to connect the cable in the box. Cables for the socket circuit in the kitchen, so the nominal load of 16 A is quite real. I decided to start the repair properly so that I could easily forget about the problem.
Cable cut, peeled about 2 cm of wires. The cable is cleaned of rubbish with a cleanser.
And a twisted pair recommended by some, and a condemned by others, and how to make it, to the best of my knowledge, properly:
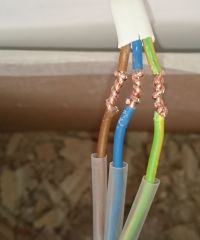
I would like to add that the cable is 2.5 mm?, so it was not twisted with your fingers. In this case, I recommend two pliers or pliers - one holds and the other curls.
I have a liking for the part of the forum in favor of a twisted pair? Or maybe the twisted pair is not like that? I admit that I pulled the zero cable slightly - I caused a part of the cable to break some 3-4 mm from the end. I have already decided to forgive this mistake and not take everything apart.
Well, now supporters of the twisted pair will begin to thunder - I do not trust the twisted pair for the sockets, there is such a machine:
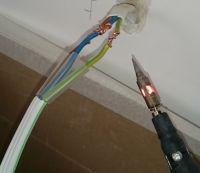
By the way - I highly recommend this solution. From getting to know gas soldering irons, I don't want to look at transformer tubes anymore. I do not know a more convenient solution (in field conditions).
And soldered:
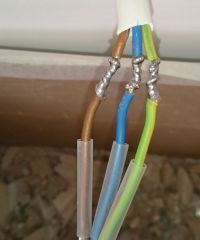
Further no surprise - cleaning:
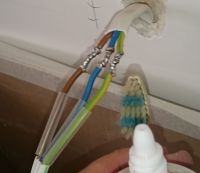
After cleaning - you probably don't see much difference in the photo, but the flux residues have been thoroughly removed:
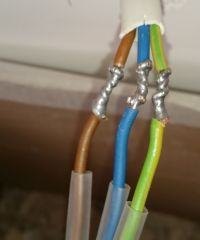
And putting on T-shirts:
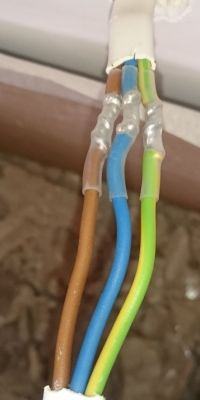
The final T-shirt to recreate the outer insulation is a T-shirt with an adhesive:
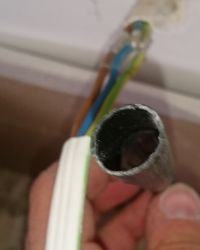
The final result:
The cable is cut solidly, in such a stupid place that I am ashamed to admit that I marked the place for a new box myself. Let's do it for fatigue and that's the end of the topic.
I decided to document the repair process so as to take advantage of this fact and officially write on the electrode how, in my humble opinion, you can properly connect the cables in the wall, if you want to avoid the box. The subject is called "roast me" because I know what writing about THESE things on the electrode can be.
Luck - the condition is such that I can easily remove and replace the cable part for the top box.
I decided to deal with the matter systematically and neatly.
For various reasons, I did not want to connect the cable in the box. Cables for the socket circuit in the kitchen, so the nominal load of 16 A is quite real. I decided to start the repair properly so that I could easily forget about the problem.
Cable cut, peeled about 2 cm of wires. The cable is cleaned of rubbish with a cleanser.
And a twisted pair recommended by some, and a condemned by others, and how to make it, to the best of my knowledge, properly:
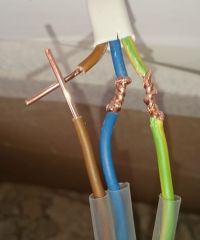
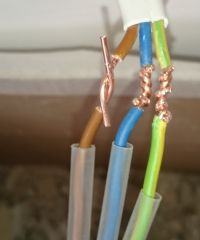
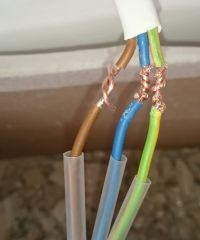
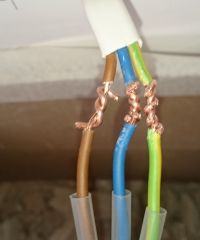
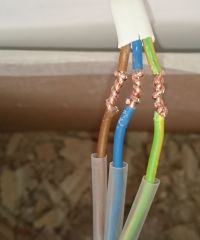
I would like to add that the cable is 2.5 mm?, so it was not twisted with your fingers. In this case, I recommend two pliers or pliers - one holds and the other curls.
I have a liking for the part of the forum in favor of a twisted pair? Or maybe the twisted pair is not like that? I admit that I pulled the zero cable slightly - I caused a part of the cable to break some 3-4 mm from the end. I have already decided to forgive this mistake and not take everything apart.
Well, now supporters of the twisted pair will begin to thunder - I do not trust the twisted pair for the sockets, there is such a machine:
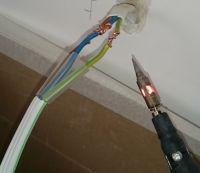
By the way - I highly recommend this solution. From getting to know gas soldering irons, I don't want to look at transformer tubes anymore. I do not know a more convenient solution (in field conditions).
And soldered:
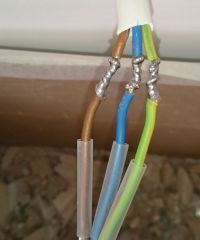
Further no surprise - cleaning:
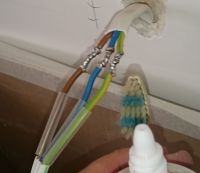
After cleaning - you probably don't see much difference in the photo, but the flux residues have been thoroughly removed:
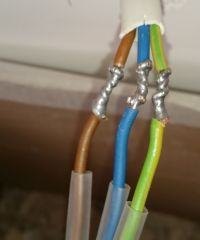
And putting on T-shirts:
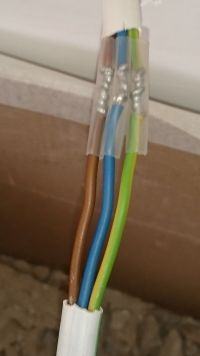
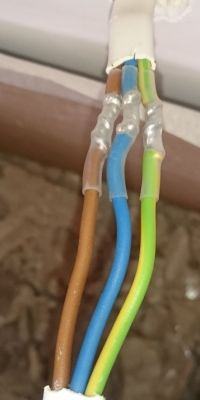
The final T-shirt to recreate the outer insulation is a T-shirt with an adhesive:
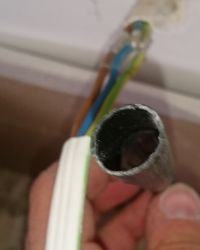
The final result:
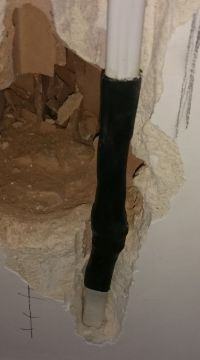
Cool? Ranking DIY